Automated manufacturing is a manufacturing method that relies on the use of computerized control systems to run equipment in a facility where products are produced. Human operators are not needed on the assembly line or manufacturing floor because the system is able to handle both the mechanical work and the scheduling of manufacturing tasks. The development of fully automated manufacturing systems dates to the later half of the 20th century, and this manufacturing technique is used in facilities of varying scale all over the world.
Historically, manufacturing was done entirely by hand. This required large amounts of labor, driving up the cost of the final product, and also exposed workers to considerable danger. During the Industrial Revolution, mechanized manufacturing was introduced. In mechanized manufacturing, workers operate equipment that does the labor, instead of laboring directly. This reduced costs, improved consistency, and contributed to developments in workplace safety. Automated manufacturing was the next step in the process of refining and modernizing manufacturing methods.
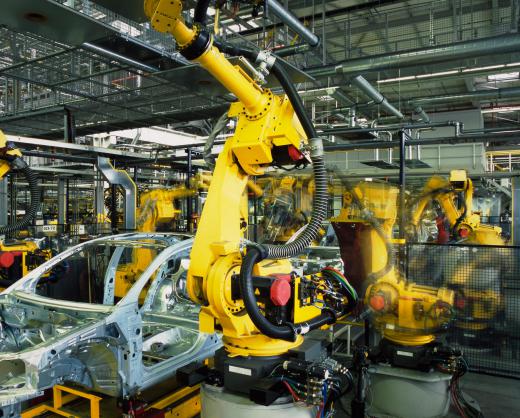
In a fully automated facility, there are no humans on the floor. Automatic equipment does the work, as ordered by control systems. These systems utilize complex software that can schedule manufacturing tasks and run diagnostics on equipment that appears to be malfunctioning. Cameras connected to sophisticated software can be used to monitor product quality, the speed of the assembly line, and so forth. Humans are involved primarily in maintenance of the equipment and programming of the control systems.
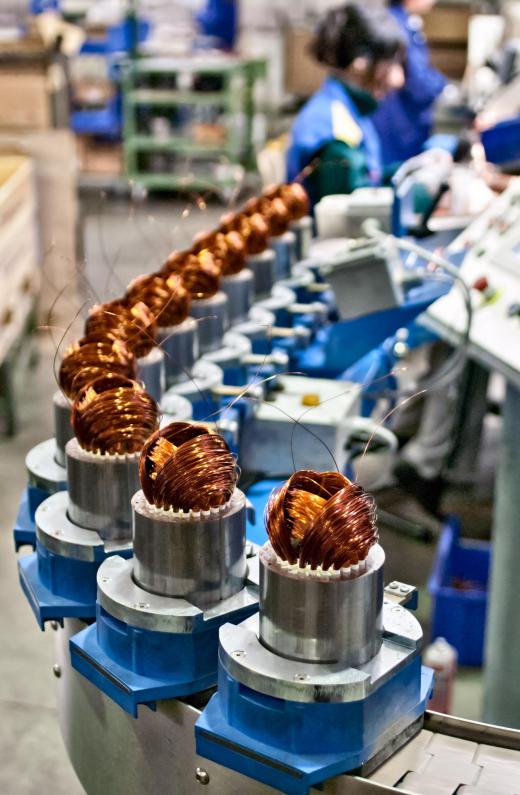
Automated equipment can fabricate, assemble, and package products. Some systems even package products for shipment complete with invoices and mailing labels, sending the products directly off the line and into trucks for shipment. The degree of automation depends on the product and the budget of the company, as automated manufacturing is expensive to implement even though it saves costs in the long term. Consulting firms can assist companies with ordering, installing, and customizing automated systems for manufacturing applications.
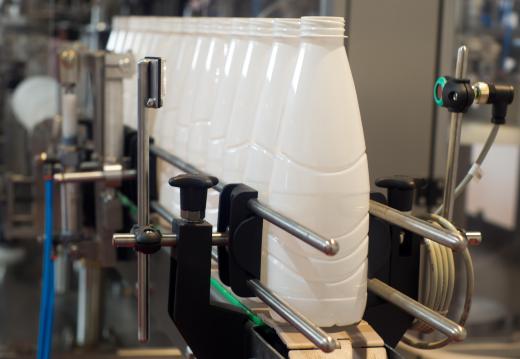
From a safety perspective, automated manufacturing is a significant improvement. If people are only on the assembly line when it is shut down to work on equipment, the risks of workplace injury decrease dramatically. Managing automated systems also requires more training and skill and translates into higher pay for workers involved in the maintenance and management of the system. Automated manufacturing also eliminates jobs, however. This has been criticized in areas where employment rates are low and people would prefer potentially dangerous manufacturing jobs to unemployment.
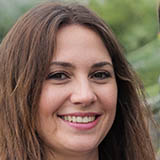
Ever since she began contributing to the site several years ago, Mary has embraced the exciting challenge of being a About Mechanics researcher and writer. Mary has a liberal arts degree from Goddard College and spends her free time reading, cooking, and exploring the great outdoors.