Automated materials handling refers to the management of material processing by use of automated machinery and electronic equipment. In addition to increasing the efficiency and speed by which materials are produced, shipped, stored, and handled, automated materials handling reduces the need for humans to do all of the work manually. This can significantly cut down on costs, human error or injury, and lost hours when human workers need heavy tools to perform certain aspects of work or are unable to perform the work physically.
Some examples of commonly used automated handling processes include robotics in manufacturing and toxic environments; computerized inventory systems; scanning, counting and sorting machinery; and shipping and receiving equipment. These resources allow humans to perform work faster, safer, and with less need for additional personnel to manage routine tasks and time-consuming aspects of producing goods from raw materials.
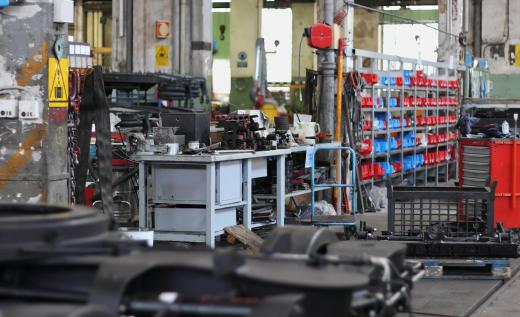
In many factories, manufacturing plants, and in areas where production requirements prevent human beings from performing manual labor, automated materials handling may be the only option. For example, it would be nearly impossible for a human labor force to assemble large numbers of automobiles entirely by hand today without the use of some automated handling equipment, such as robot assembly devices and tracks that carry the automobile shells from one end of the factory to another.
In addition, it would be physically impossible for a team to transport, lift, and keep track of heavy containers full of materials and place them in storage areas or truck beds without the use of automated material handling resources like lifts, cranes, or trucks. Automated systems use tracking devices to scan and check materials in or out, and this information is automatically linked to computers that tell the factory management when to order more materials, where materials are stored, and where to allocate and ship materials. These automated handling tools are commonplace in most warehouse, trucking, and manufacturing environments because they increase productivity and reduce waste.
Automated materials handling is not new to manufacturing and materials management. It has been in place since the turn of the 20th century, when mass production necessitated the use of heavy machinery to turn raw materials into useful products for consumer and commercial use. Automated handling is now commonplace among many companies that process materials into other goods and will continue to develop, thanks to continual advancements in technology.