A flexible manufacturing system (FMS) is a type of industrial process that allows equipment to be used for more than one purpose, though they may be somewhat related. The equipment is often used to make customized parts, or make different parts for different models of product. This type of system may be changed by hand, but is more likely to be controlled by a computer, and changed through an entirely automated process.
The main goal of a flexible manufacturing system is to offer the speed needed to change with market conditions quickly, but not sacrifice any quality. Equipment that does this most effectively is likely designed for two or more purposes. While it may be possible to modify or retrofit some types of industrial equipment to do a job adequately, most FMS are designed for more than one purpose from the very outset.
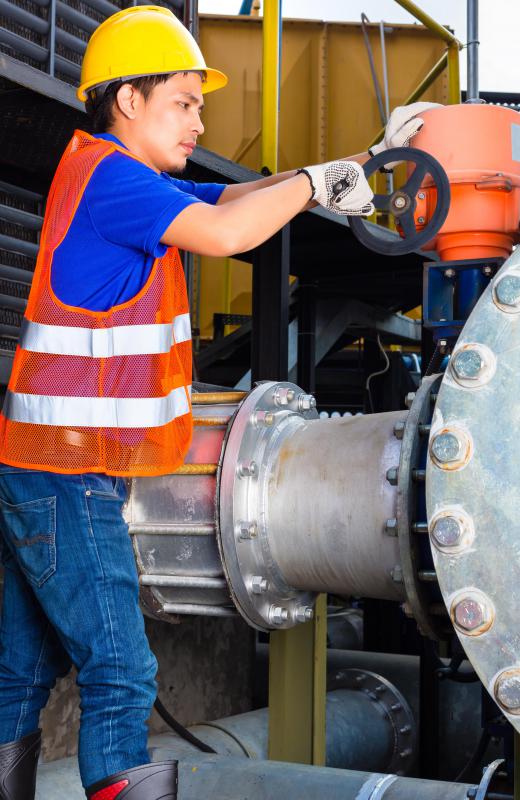
Though the equipment for a flexible manufacturing system may initially be more expensive than traditional equipment, the overall goal is to reduce expenses. Manufacturers can save money by using the same equipment to essentially perform two or more functions. With traditional equipment, manufacturing two different products may not only require different pieces of equipment, but also two different lines and perhaps two different facilities. Therefore, this type of system may reduce overhead, despite higher start-up costs initially.
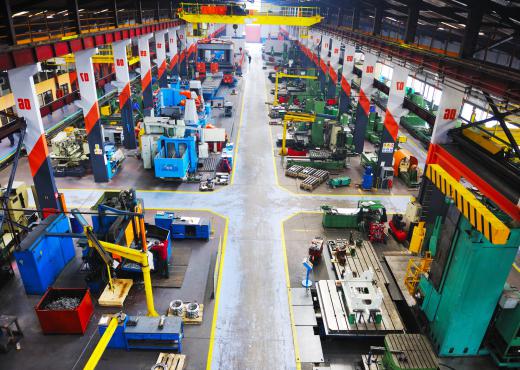
One of the most common examples of a flexible manufacturing system can be seen in the manufacturing of automobiles. Certain equipment is used to attach doors to a sedan. With just a few simple adjustments, that same line and equipment may be used to attach doors to a sport utility vehicle or some other type of vehicle. Often, the switchover can take place with very little disruption to the line, and may even happen during shifts.
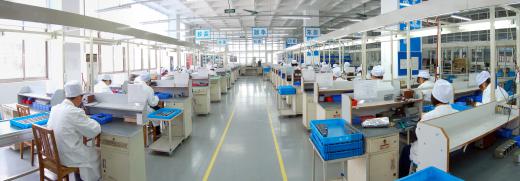
In fact, the automobile industry can potentially save a substantial amount of money using a flexible manufacturing system. A report in 2004 indicated that Ford Motor Company saved approximately $2.5 billion US Dollars by putting flexible systems in at five manufacturing plants. The company estimated it can save at least half of the cost of manufacturing updated models using the systems.
In some cases, the machines may not only be used to produce or assemble different parts for different models, but to make customizations. These customizations, without a flexible system in place, would take much longer, and be much more expensive for the customer. Using machines with the ability to be flexible can not only speed the process up, but can improve customer satisfaction by bringing down the price.