An assembly line is a type of industrial production in which prefabricated, interchangeable parts are used to assemble a finished product. The most basic assembly system consists of a simple conveyor belt which carries the product, such as a toy, through a series of work stations until it is finished. More complex lines include feeder belts to carry parts to work stations along the line, used for building cars and other complex equipment. The development of the assembly line revolutionized manufacturing, and contributed to the substantial fortunes of several major players in the Industrial Revolution.
Before the advent of the assembly line, when a commercial good was manufactured, it was usually created by hand, from individually fabricated parts. Factory production was limited by available floorspace, as only so many products could be made at once, and workers tended to see a project through from beginning to end. By the mid-nineteenth century, many companies in the food industry had begun to set up something resembling an assembly line to make the process more efficient, but it was not entirely streamlined. Goods like the early automobile and steam engines were still made by hand.
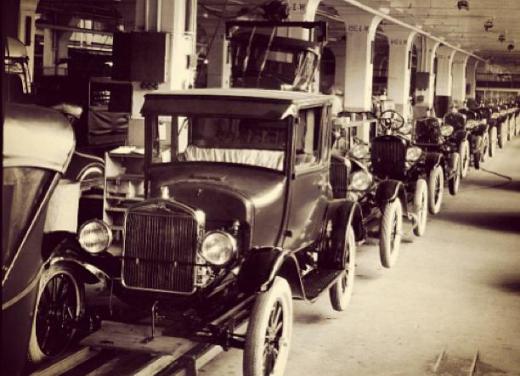
In 1908, Henry Ford was trying to find a way to bring automobiles to the masses. Ford was confident that if the cars could be made affordable, they would become popular, but the slow and painstaking method of manufacture being used did not allow Ford to bring the cost of the cars down. Working in consultation with others at the company, Ford conceived of a production line, where the labor of workers would be divided into specific tasks which would contribute to the finished whole. The inspiration for this early assembly line likely came from several industries, but many historians credit the disassembly line at a Chicago slaughterhouse with the idea of dividing the labor.
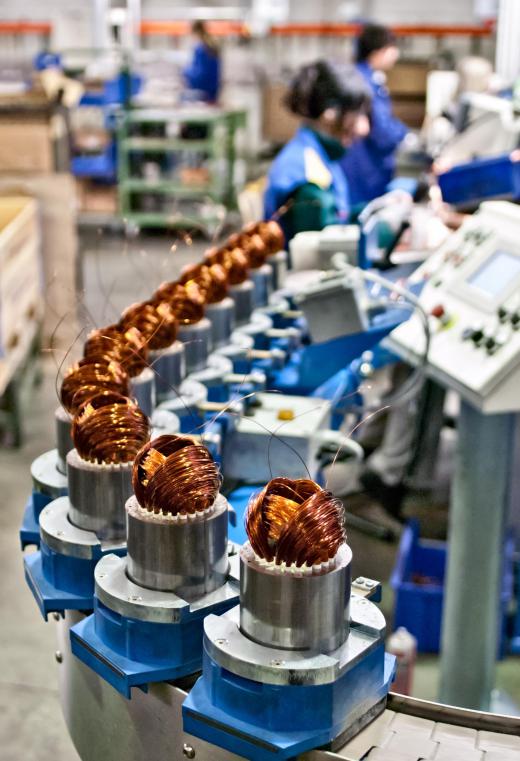
An assembly line is designed to be highly efficient, and very cost effective. The workers focus on a small part of the overall whole, meaning that they do not require extensive training. Parts are fed along a conveyor belt or series of belts for workers to handle, creating a continuous flow of the desired product. At the peak of production, Ford's line turned out a new automobile every three minutes, and modern lines can be even more rapid, especially when they combine automated machinery with human handlers.
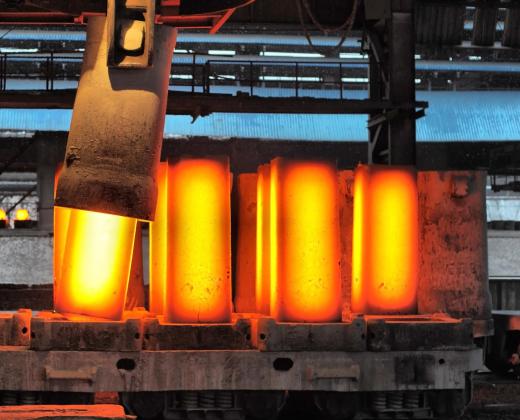
There are dangers associated with an assembly line. The first is the risk to workers, as repetitive movement can be harmful to the body. After the Second World War, a growing awareness of this issue led to reforms in assembling environments. The second issue is that if there is a snarl in production at one work station, it will have an impact on the entire line, potentially bringing it to a halt until the situation can be fixed. However, most modern manufacturers work to prevent this with regular inspection, and some manufacturers, especially of cars, welcome worker input and thoughts on ways to make the assembly line, and the product, better.
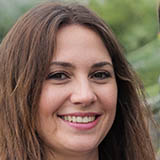
Ever since she began contributing to the site several years ago, Mary has embraced the exciting challenge of being a About Mechanics researcher and writer. Mary has a liberal arts degree from Goddard College and spends her free time reading, cooking, and exploring the great outdoors.