Wave soldering is an automated process in which components are soldered onto a printed wiring board (PWB) as the board passes over the top of a wave of solder. Air pumped up from the bottom of a container of melted solder creates this wave. Baffles mounted inside the pot also help to form the required wave profile for the board being soldered.
A PWB being assembled with a wave soldering process undergoes three basic stages. In the first stage, the underside of the board is evenly coated with a material known as flux. This is typically applied as a spray or foam. Flux prevents oxidation from being produced at high temperature and impeding proper solder application to the parts being soldered.
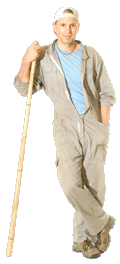
Preheating follows fluxing in order to dry and activate the flux in preparation for soldering. It also reduces the thermal shock the board and components experience when they pass over the hot wave of melted solder. Dissipation of volatile materials in the flux in this stage reduces the likelihood of spattering while the board is being soldered. This reduces the number of opportunities for the creation of solder defects in the final product.
Once preheated, the PWB passes on a conveyor over the wave such that solder is applied to leads, terminations, and other areas on the bottom of the board. No solder flows onto the top of the board. Areas on the board that are not to be soldered are typically coated ahead of time with solder mask to prevent solder from adhering to them.
Many manufacturing facilities use wave soldering because the process can create several thousand solder joints in only a few minutes. This helps the facility achieve a much higher rate of production than would otherwise be possible. The wave soldering process does, however, pose some challenges in a production setting. Since the rate of production of boards is high, there is also great potential for quickly producing a great deal of defective hardware due to poor process control.
The solder connections formed by the wave soldering process not only attach the components to the board, but also form electrical connections between them. This is what allows the final product to function electronically. Soldering defects are not only a cosmetic concern. They may also result in the board not functioning properly or possibly even being damaged beyond repair.
In order to produce circuit boards of consistently high quality, many variables must be carefully designed and tightly controlled. The geometry of the wave profile must be properly maintained to avoid applying excess or insufficient solder. Control of preheating and soldering temperatures is necessary to ensure that no damage is done to the PWB or the components on it. Maintenance of a clean manufacturing environment helps ensure solder and flux purity, thereby reducing the risk of defective hardware.