Filler metal refers to any material used to join two pieces of metal during welding or soldering. As the two objects are held together, filler metal is melted between the two to create a bridge. After the filler dries, it combines with the objects on either side to create a permanent bond.
The filler materials used in metal-joining come in a variety of forms to suit the needs of different projects. Covered electrodes consist of solid metal rods coated with alloys or protective coverings. These metals are used in stick welding, or covered arc welding, which is one of the most basic welding techniques. During this process, the stick of filler metal is held within the area of the weld. As heat is applied to the area, the stick of metal melts to fill the gap between the two. Covered electrodes typically consist of things like carbon steel or chromium-coated steel, which is used to enhance corrosion-resistance in the finished product.
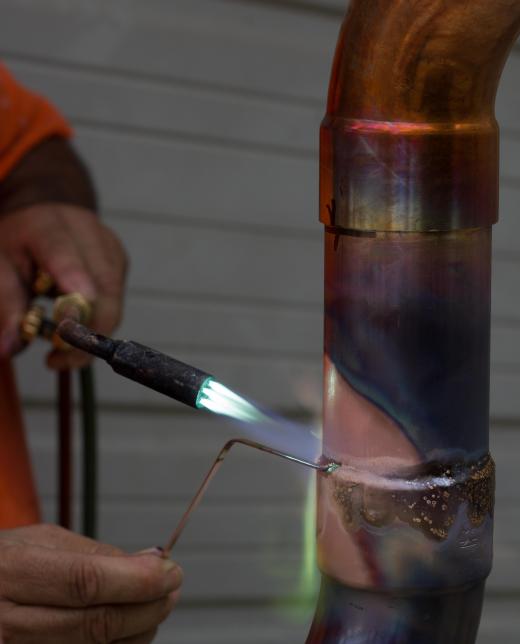
Bare electrodes are another form of filler metal, and are commonly used during gas-shielded arc welding. The metal itself consists of metal wire coiled within a wire feeding device. During welding, the user feeds wire through the shielded welder to join two metallic objects to one another. Bare electrode wires often are made of metals like copper, tin, lead, or nickel.
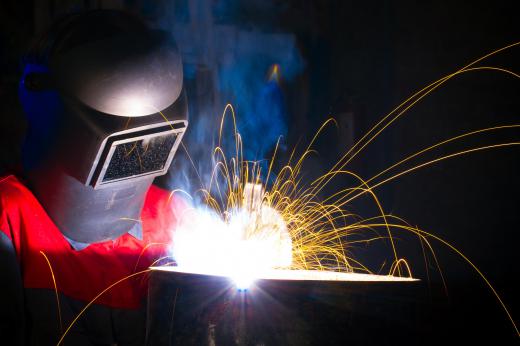
Welders looking for a filler material may also choose flux, which is used in submerged arc welding. During this process, the flux covers the entire arc as the two materials are joined. By covering the welding arc, flux fillers protect the user from sparks, flames, and other welding-related dangers.
When selecting a filler metal, workers must decide how the tensile strength of the filler should compare to the tensile strength of the metal. When the strength of each is relatively equal, the filler is said to be matched to the metal. Filler that is weaker than the surrounding metal is said to be undermatched, which may help reduce the risk of cracking or failure in high-strength materials. Filler that is stronger than the surrounding metal is considered overmatched. Overmatched filler metal offers high strength in some applications, but also comes with a high price tag, and may not be suitable for all projects.
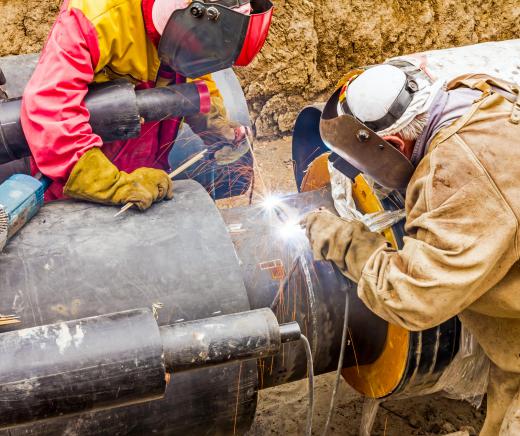
In addition to matching the strength of the material, workers must consider a number of other factors when choosing a filler metal. The form of the metal objects, as well as the material they are made from can impact filler selection. This decision may also be influenced by the fire or corrosive-resistance of the metal, as well as the type of welding technique being used.