An automated storage and retrieval system is an inventory management system that relies on computers and robotics for its operation. Utilized by distribution, manufacturing and storage facilities, they are costly to design and install, but can be highly accurate in terms of inventory control, and can provide significant savings in all cost centers associated with inventory management and distribution. An automated storage and retrieval system may be employed for a wide variety of purposes, such as storage of archival documents, small parts storage and management, storage of raw materials until needed, and storage of finished product awaiting sale and shipment.
While many automated storage and retrieval systems are found in industrial facilities, there are many commonly known systems of automated storage and retrieval that are used daily by consumers worldwide &emdash; consider the photographic slide carousel used in conjunction with a slide projector, on which slides are stored in order and retrieved mechanically for individual display. A more advanced consumer application of an automated storage and retrieval system is the common vending machine &emdash; items for sale are loaded, and then automatically retrieved upon selection by the consumer.

By contrast, an example of a completely manual storage and retrieval system is a grocery store, where shelves are loaded by hand with items for sale, and taken from the shelves for purchase by the ultimate consumer. Two of the most significant features of an automated storage and retrieval system are the vast reduction of time necessary to accomplish the tasks of accurately storing or retrieving items, whether for internal or external use, and the vast savings of space realized when human-based dimensions such as corridor width no longer must be accommodated.
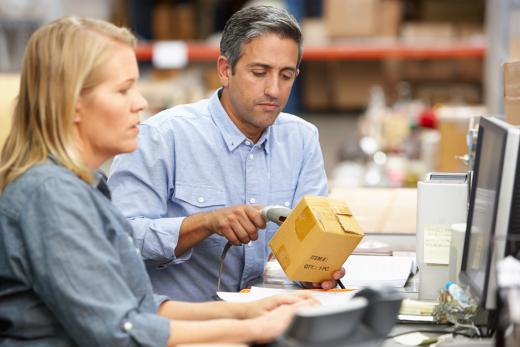
An automated storage and retrieval system designed for use in a distribution, manufacturing or storage facility will generally be much larger than a slide carousel or vending machine, often installed floor-to-ceiling in warehouse-sized facilities. A fully automated system may include tracks on the floor or suspended from the ceiling to guide robotic machines as they move from location to location, storing or retrieving materials. The items stored may be in their own packaging, such as film canisters or sale-ready consumer goods in cartons, or they may be in containers, such as small machine parts in pans or buckets. When “picking” multiple items for shipment to a customer, an operator will enter the items' identification codes into a computer, which will identify the items' location and instruct a machine to retrieve them and deliver them to another location where they'll be packaged for delivery to the customer.
There are many features and benefits of an automated storage and retrieval system that make it a very desirable alternative to manual storage and retrieval, such as the vastly improved inventory management and tracking, reduction in personnel and the associated workplace accidents and injury, reduction of time required to retrieve material and fill customer orders, and more efficient use of storage space, to name just a few, all of which lead to significant cost savings.
There are drawbacks that aren't so easily anticipated, though. The system itself will require ongoing maintenance far beyond what would be required by a manual system of steel shelving. All moving parts will need routine inspection and maintenance, such as calling for qualified mechanics, and aging machinery will eventually require replacement. The software responsible for managing the inventory and operating the storage and retrieval machines also must be maintained and periodically updated, and of course the system's human operators and their managers will require more training to learn and keep current with the technology.
Despite all the drains on a company's resources represented by an automated storage and retrieval system, their ever-increasing popularity is ample proof that their features and benefits outweigh their drawbacks, however, as they become more of a staple than an oddity in even small- and mid-sized operations.