The glass manufacturing process can be traced back to 3500 BC, when ceramic pottery was coated with a glass surface glaze. While there are many modern variations on the glass manufacturing process for industrial and scientific uses, traditional glass used to make windows, food and drink containers, and ornamental shapes is still made from the same three ingredients used in ancient times. These are sand, alkali-based sodium bicarbonate referred to as "soda ash," and lime from limestone. These three main ingredients are fused together in a furnace at a temperature of around 2,500° Fahrenheit (1,371° Celsius), after which several minor ingredients can be added to alter the glass color or brilliance. It is then cooled several hundred degrees so that it can be shaped by blowing, pressing, or drawing into pipes, bowls, mirrors, windows, and more.
Introducing soda ash into the glass manufacturing process was discovered early on as a way to lower the initial melting point down from a peak of around 4,100° Fahrenheit (2,200° Celsius) to 2,700° Fahrenheit (1,482° Celsius). Soda ash, however, makes glass somewhat water soluble, so lime from limestone was added to prevent this, and other chemicals such as aluminum oxide are now substituted for lime as they offer greater chemical stability. Soda-lime glass still accounts for 90% of all manufactured glass.
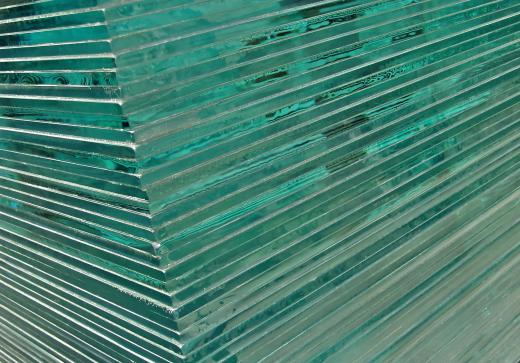
As glass is cooled, it becomes easier to shape into forms, but it must continually be reheated during the glass manufacturing process to add strength to it to avoid shattering. This procedure is known as annealing. An additional tempering process to strengthen the glass is also employed by reheating it and then cooling it suddenly with blasts of cold air.
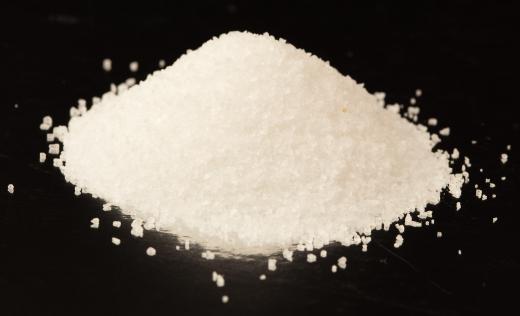
The most common shaping method in the glass manufacturing process in ancient times involved blowing air into a ball of molten glass at the end of a long, hollow pipe, which the Romans perfected for making beautiful vases and bowls. Float glass manufacture, invented in 1959 by a British company, is the largest current production method done by pouring molten glass into a tank with melted tin on the surface. The glass floats on top of the tin and forms into extremely smooth sheets which can then be cut into window shapes. Dolomite is often included in sheet glass manufacture at levels below 0.1% to maintain the colorless quality of the glass. Drawing a stream of molten glass around the inside of a metal cylinder as it rotates and air is pumped in, is another frequent glass manufacturing process used to make a wide array of glass pipe for light bulbs, vacuum tubes, and glassware used in laboratories.

Other types of specialized glass include lead glass, which contains at least 20% lead oxide and is brilliant when cut and faceted. Heat-resistant glass products used in cooking bowls and labware are made by adding 5% boric oxide or aluminosilicate compounds. Colored glass products are made by adding iron sulphides for brown and amber colors, iron chromate for green shades, and white cobalt for shades of blue. Natural blown glass has a red to orange color without requiring any chemical additives.