Stud welding is the process by which heat created with an electrical current is used to join a metal fastener to another piece of metal. This type of welding is widely used in the manufacture of products composed largely of metal, such as automobiles and ships. There are two types of stud welding: capacitor discharge (CD) welding, which is most often used to join small fasteners to a thin metal base, and arc stud welding, which is usually used in joining large fasteners to a more substantial metal base.
The fasteners used in stud welding come in a wide variety of shapes and sizes, some which resemble regular nuts, bolts, or studs. Unlike normal fasteners, however, the ends of these pieces are specially designed for CD or arc stud welding purposes. Those designed for CD welding have a flat collar on the weld end with a projecting tip that breaks down as electrical current is applied, facilitating a strong weld. The fasteners used in arc stud welding sometimes feature aluminum on their weld end, again helping to create a solid bond.
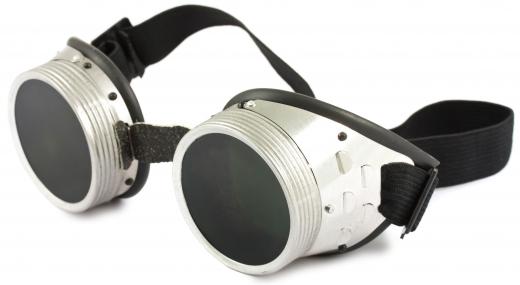
As the CD welding process takes just milliseconds, it can usually be done without causing visible heat damage to the metal onto which the fastener is being joined. To perform a CD weld, the specialized fastener is first loaded onto the welding gun and then placed against the metal piece to which it will be welded. The welder starts the gun, sending an electrical current to the fastener and metal piece, which results in the creation of heat. This heat causes the fastener’s tip and collar as well as part of the metal piece to melt. A spring within the welding gun then drives the fastener into the metal piece, and as the melted substances cool they are fused together.
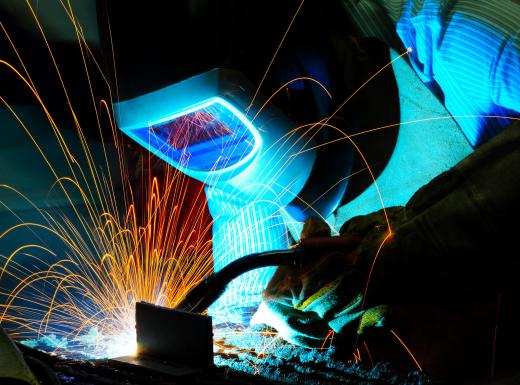
Arc stud welding is used to join fasteners and metal pieces that are too large or thick for CD welding. As with CD welding, the arc stud is loaded onto a welding gun, but the before it is placed to the spot where they will be joined, that spot is surrounded by a ferrule, or ceramic ring. This ferrule contains the heat created by the weld, preventing the metal around the weld area from melting. The welder then starts the gun, which emits an electrical current that melts the stud tip as well as the base metal within the ferrule, and then forces the fastener into the base metal. After the metals have cooled and fusion has been achieved, the ferrule is usually chipped away.
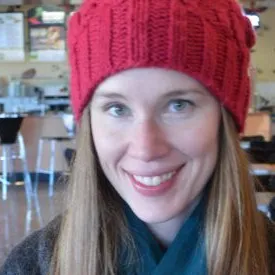