Welding refers to a process that is used to join two metal objects. Spot welding is a form of welding that requires a unique welding machine. This machine is designed with clamps that join two pieces of metal together with electrodes. The electrodes are used to apply pressure and electricity into the metal objects. This causes a spot weld to be formed with a metal nugget between the objects.
Elihu Thomson invented spot welding in 1877. Mr. Thomson had determined that two sheets of metal could be fused together by applying pressure and electricity to a discrete point. As the voltage is pumped into the metal material a nugget of melted metal is formed that is used as an epoxy element, securely binding the two objects. This type of welding is most often used by large robotic devices when creating automobile body parts.
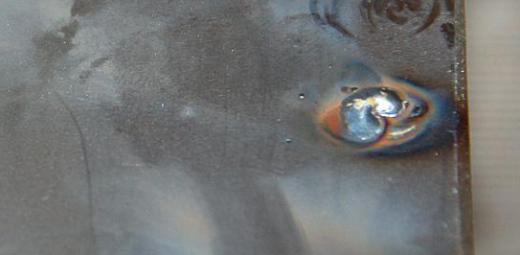
There are many types of spot welding machines available today. These include both large floor-mounted welders and small portable welders. Each type of welder includes an electrical power supply and special electrode rods. The size of the weld nugget depends on the thickness of the electrode rods and the amount of pressure and time they are placed on a object.
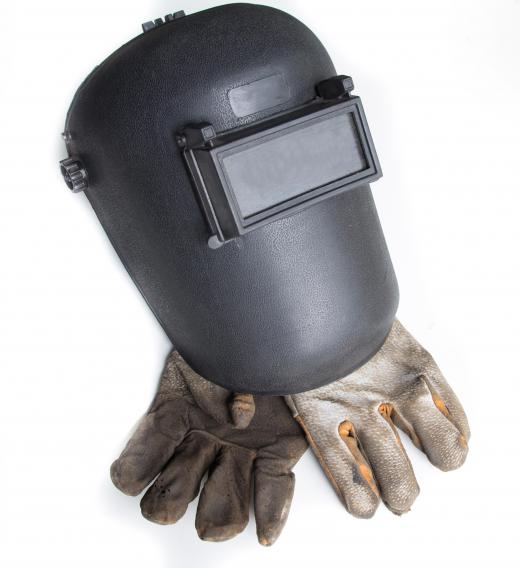
Most welding generates extreme heat and high light illumination. This light can cause temporary and long-term blindness. It is recommended to wear a welding safety helmet that includes significant darkening lenses. This is similar to extremely dark sunglasses.
Welding is a dangerous occupation that also requires other special safety equipment. This includes gloves, fire resistant clothes, along with the aforementioned glasses. When the objects are fused together, hot metal may shoot into the face or clothing of the welder. Without safety equipment, this could result in serious injury.
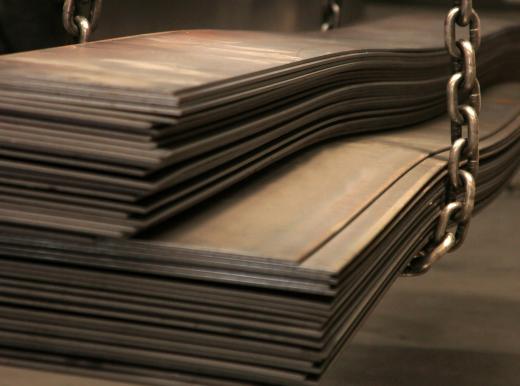
Welding is an art that requires a basic understanding of physics and metal composites. Each type of metal requires a specific volume of welding area to hold. This spot welding is based on both the size and type of the material being welded together. Some examples of material include steel, aluminum and copper. Each has a specific pressure and time requirement for a spot weld.
Mig spot welding is a form of welding that requires penetration of one of the metal objects before the fusion begins. This type of welding is known as plug welding because the penetrated area is plugged with melted metal material. Mig welding has only been available within the last few decades and offers a comparable welding option.