Rapid prototyping is a computer program that constructs three-dimensional models of work derived from a Computer Aided Design (CAD) drawing. It is used to quickly and easily turn product designs into physical samples. The creation of physical samples with this method is achieved through Adobe Portable Document Format (PDF) and CAD formats, as well as through cross-functional teams and integration.
The rapid prototyping method was first introduced to the market in 1987, after it was developed with the help of stereo lithography. Today, it is also known as solid freeform fabrication, 3-dimensional printing, freeform fabrication, and additive fabrication. The manufacturing process of rapid prototyping can produce automatic construction of physical models with 3-dimensional printers, stereo-lithography machines, and even laser sintering systems.
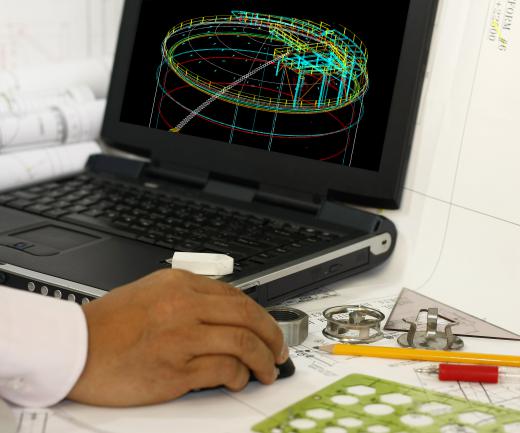
Using a CAD drawing to create a physical prototype is quite simple for the user. First, the machine reads the data from the provided CAD drawing. Next, the machine lays a combination of liquid or powdered material in successive layers. The materials used in rapid prototyping are usually plastics, ceramics, wood-like paper, or metals such as stainless steel and titanium.
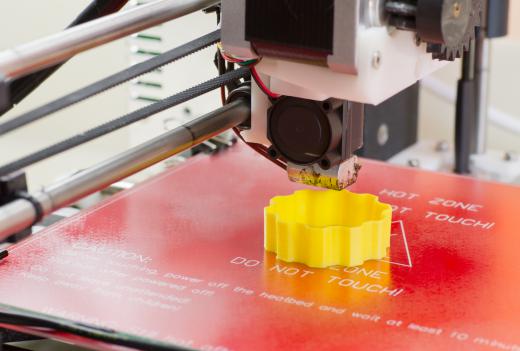
With rapid prototyping, each layer is built to match the virtual cross section taken from the CAD model. Therefore, the final model is built up gradually with the help of these cross sections. Finally, the cross sections are either glued together or fused with a laser. The fusing of the model automatically creates its final shape.
Rapid prototyping is necessary for those who want to create models for clients, such as architects and engineers. It can reduce the design cycle time, allowing multiple tests to be performed on the design at a low cost. This is because each prototype can be completed within days or hours, rather than taking several weeks. In addition to engineers and architects, other professionals benefit from rapid prototyping, such as surgeons, artists, and archaeologists.