Flux cored arc welding (FCAW) is an automated or semi-automated arc welding process utilizing a consumable, hollow electrode filled with flux. FCAW machines typically run on a constant voltage power supply although some examples utilize constant current supplies. There are two basic types of FCAW: one that uses an external shielding gas supply and one that relies on the flux content of the electrode to ensure surface protection. Flux cored arc welding is suitable for a wide range of metals and holds several advantages over shielded metal arc welding processes. These include high weld speeds, less pre-cleaning of workpieces, and a broad range of practical weld positions.
Conventional manual or shielded metal arc welding (SMAW) processes utilize individual, flux covered electrodes to generate the arc. Flux cored arc welding makes use of a continuous, consumable electrode which is hollow in cross section and filled with flux. The electrode is wound on a drum or spool on the FCAW machine. As the electrode is consumed at the weld point, the machine advances the electrode spool, thus ensuring continuous electrode contact.
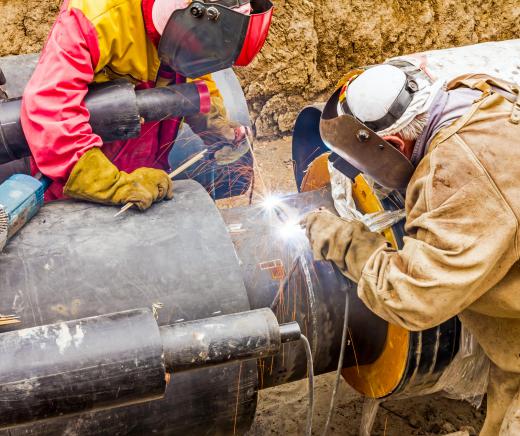
FCAW machines run on either constant voltage or constant current power supplies. On constant voltage machines, the voltage is set and the current or arc amperage can be manipulated to suit the job requirements; constant current machines feature a set amperage. The two main types of flux cored arc welding machines are those utilizing external shielding gas supplies and those that rely on the flux core of the electrode alone to protect the weld surface from oxidization.
The flux cored welding process is fairly flexible and offers several variables which may be manipulated to suit job requirements. These include the extension lengths of the electrode and the speed at which the electrode feeds. The electrode angle and physical travel speed can also be adjusted. When external shielding gas supplies are used, there is also a selection of shielding gas compositions to choose from.
The FCAW process holds several advantages over manual arc welding. Flux core welders can be used in a range of positions which are impractical with SMAW processes. Welding speeds are also higher with less pre-cleaning of weld materials necessary. The electrode design of flux cored arc welding machines also allows for efficient welding in windy outdoor conditions without having to use a shielding gas. One point that should be remembered in this regard is that gases given off by the process in the absence of a shielding gas may be extremely toxic and require forced ventilation.