Automatic welding is also called robotic welding. The advancements in technology have allowed robots to take over skilled trade positions in manufacturing facilities all around the world. When a product that has been riding along an assembly line comes to a halt in between welding robots, the robots begin automatic welding sequences which have been programed into a control system. The benefit in automatic welding is a perfect weld every time without human error.
As the development of the wire welder improved, the design of automatic welding robots also got better. The wire spool permits hours of welding without requiring a spool change. The computer programing that controls automatic welding stations is so advanced it is able to correct any problems detected without human assistance. By using automatic welding robots, a manufacturer is able to avoid costly ventilation systems and breathing apparatuses required for human welding personnel.
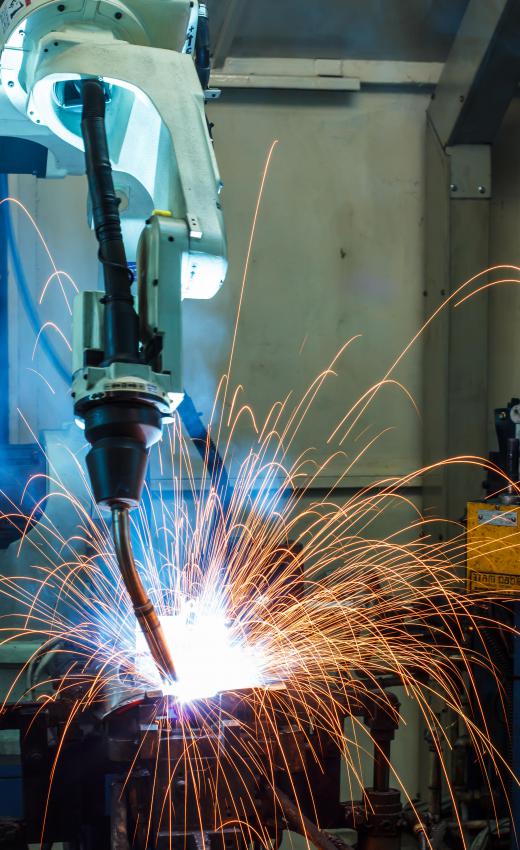
In the early years of manufacturing, a human welder was required to perform the welding operation. Welding machines used replaceable welding rods that required changing as they burned down. The toxic smoke and gases produced through welding began to create health problems linked directly to welding. This required the use of welding respirators that would filter out the toxins. The earliest form of the respirator was uncomfortable and hot and required frequent breaks to avoid exhaustion by the wearer.
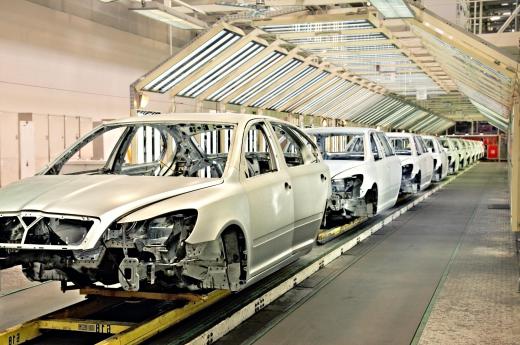
For many years, it was thought that men could do a better job on an assembly line than machines. As the machines began to improve and labor costs went up, components such as automatic welding robots began to dispel the myths concerning unreliability and robots. The auto industry was one of the first to fully encompass the automatic welding robot. A series of robots was soon tasked with completing all the welding sequences required to create an automobile. The repair and rework requirements were reduced, and soon there was little need to man a repair crew for the assembly line.
Prior to the introduction of the automatic welding robots, a repair crew was required to fix mistakes made by human welders. The machines proved competent in completing proper welds with correct penetration and proper start and stop points. Unlike its human counterpart, the robot welder is able to hit its beginning mark exactly and complete a flawless weld at the proper speed and temperature nearly every time. The ability to eliminate repair work due to human error allows the manufacturer to reduce project costs.