Cold working is a type of metalworking done by subjecting metal to enough mechanical stress to cause plastic deformation, a permanent change in the metal's crystalline structure. It gets its name because it is done at temperatures below the metal's recrystallization point and alters the metal's structure through mechanical stress rather than heat. The technique increases a metal's strength and hardness while reducing its ductility. A number of different processes are used in the modern metalworking industry that are applied to materials such as steel, aluminum, and copper.
This type of metalworking strengthens the material through a process called work hardening or strain hardening. When the mechanical stress on a metal becomes high enough, it causes permanent crystallographic defects, called dislocations, in the crystalline structure of the metal's atoms. As the number of dislocations increases, it becomes more difficult for new ones to form or for the existing defects to move through the crystal structure, making the metal become more resistant to further deformation. This increases its yield strength and allows it to withstand greater stress, but it also means that the metal becomes less ductile and that, if the metal is subjected to too much stress, it will fracture rather than bend.
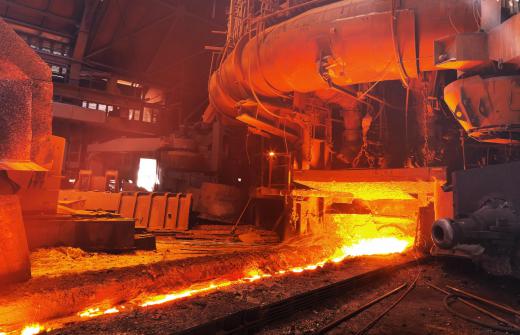
Cold working is often more cost effective than working metal through heat treatment, especially for large-volume production, because it produces comparable improvements in strength while using materials more efficiently and requiring less finishing. The high initial capital cost of this process, however, makes it less cost effective than heat treatment at smaller scales. The lower ductility of cold-worked metal also makes it inferior in some applications. Its higher resistance to deformation makes it less able to give way to forces the metal is not strong enough to resist, and so if the metal is subjected to too much stress, it can fracture rather than bend. Some metal production uses both methods at different points in the production process to impart the desired qualities in the metal.
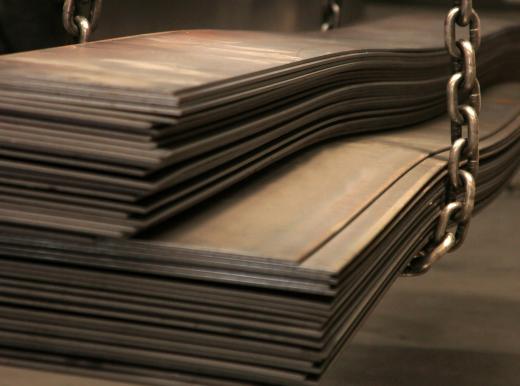
There are a number of different methods that can be used for cold working. The most common type is cold rolling, in which the metal being worked is squeezed through narrow gaps between rotating metal rolls. The movement of the rolls compresses the material, causing deformation as moves it through the gap. Another method is cold forging, in which metal is shaped by forcing it into a die with a press or hammer.