There are numerous types of production line equipment, including printed circuit board (PCB) assembly machines, computer numerical control (CNC) machinery, lathes, and extrusion devices. Each piece of machinery must be controlled and calibrated to manufacture the necessary product for distribution; poorly maintained machines often generate inaccurate and malfunctioning finished goods. Workers with great attention to detail normally examine all products that are formed by their particular machine.
Most electronic finished goods, such as a cell phone, have some form of PCB within their internal structure. As a result, many manufacturing facilities must have production line equipment that can create a board from raw materials. The board must have a solder paste machine applying its circuit pathways, while another device picks and places electronic components onto the newly created solder pads. PCBs must enter a reflow oven to melt the solder with the components; afterward, the board is thoroughly tested with an optical bond tester machine.
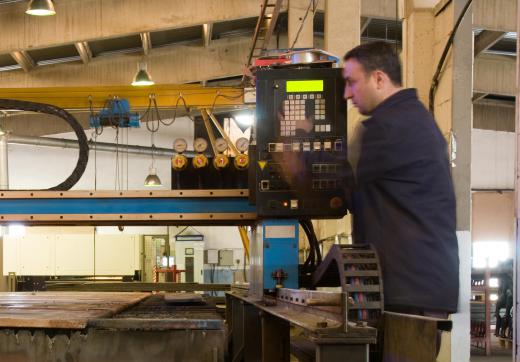
CNC production line equipment creates mechanical parts for items as varied as vehicle axles and bicycle frames. An operator programs the machine through computer commands; the machine responds by drilling or cutting a piece of raw material, like metal, into a specific shape. These computer-controlled machines produce a part with accurate dimensions for mass manufacturing. For example, multiple vehicles can be produced in a single day with the rapid production of parts compared to a hand milling manufacturing strategy.
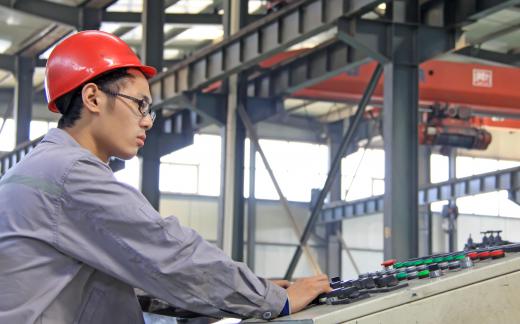
Lathes are specialized pieces of production line equipment that rotate an item in a horizontal position. This spinning action keeps the raw material item in a fixed, horizontal position so that it can be sanded or cut. For example, a wooden dining table leg can be placed on the lathe so that intricate shapes can be cut into the wood for a pleasing aesthetic appearance.
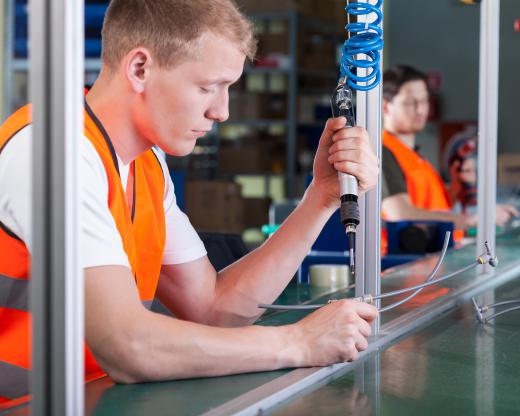
Extrusion production line equipment uses molten plastic forced through a nozzle to create items, like device housings. An operator must monitor and adjust the machine so that the plastic material stays within a specific temperature range, allowing it to flow evenly through the extrusion process. Any defective items that extrude from the machine, such as housings with multiple holes, must be isolated, and the operator must stop and troubleshoot the machine until the problem is resolved.
Each production line machine is operated and regulated by trained personnel. Workers must check and calibrate the machine periodically for the best product output. In general, these employees must be comfortable with computers since the majority of the machines are controlled primarily by software programs.