A forming limit diagram (FLD), also known as a Keeler-Goodwin diagram, is a graph that illustrates the behavior of sheet metal under different levels of strain. The line describing the behavior of the metal is called a forming limit curve (FLC). A forming limit diagram provides information on the maximum stress the metal can undergo before fracturing or necking. The diagrams are constructed by using test strips of sheet metal and measuring the deformation.
Forming limit diagrams are graphed in a two-dimensional coordinate system, with the major strain plotted on the y-axis and the minor strain plotted on the x-axis. Strain is a measure of the deformation — major strain is defined as being in the direction with higher deformation, while minor strain is in the direction with less deformation. Different types and different thicknesses of sheet metal each have their own unique forming limit diagram.
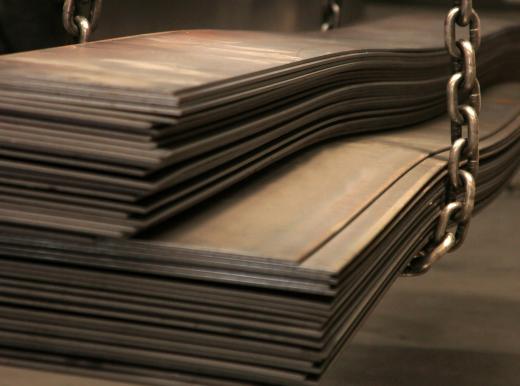
An FLC is an irregular parabolic curve, with the minimum occurring at or near the major strain axis. A material subjected to strains that lie above the curve will fail, while strains below the curve are safe to apply to the metal. FLDs are usually graphed with two curves — the area between the curves is a zone of critical deformation or safety zone, where the material may be safe or may crack, so in practice it is best not to apply those strains. The critical deformation that is likely to occur in this zone is called necking, which is when the metal is stretched thinner in some areas.
A forming limit diagram is developed using a series of tests. During the tests, strains are applied to metal strips of differing widths. The different widths of strips simulate different strain conditions. Each strip is marked with a circular grid pattern that is used to measure the strain.
Strain is usually applied to the strips using a hemispherical punch. A metal strip is stretched until necking is observed. Strain values for the major and minor axes can be obtained by measuring the deformation of the circular grid previously marked on the strip.
Computer-based methods may also be used for measuring strain. Images taken by the computer during the deformation process can be compared to a reference grid comparable to the circular grid on the metal. The computer can compute the strains using these images. Another method compares before and after images of the circular grid in order to calculate strain.