Board-to-board connectors are indispensable miniature coupled plugs and sockets that directly connect power and signal between printed circuit boards (PCBs). They are usually in-line or connector pins in a straight line. Board-to-board connectors usually use copper alloy that resists oxidation to prevent degraded conductivity over the years.
In electronics manufacturing, an entire device or equipment may need to fit a certain available space such as 19-inch (0.5 m) wide racks. If the PCB in the circuit board design stage tends to use up too much space, the device may be split into two or more boards. Board-to-board connectors may join power and signal between the boards to complete all connections.
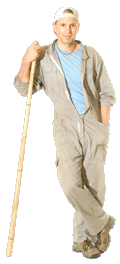
The use of board-to-board connectors simplifies the circuit board design process. Smaller PCBs would require manufacturing equipment that may not accommodate a combined bigger PCB. Whether a device or product will be squeezed into a single PCB or multiple PCBs is a question on power dissipation, undesired intercoupling of signals, availability of smaller components, and overall cost of finished device or product, among others.
Moreover, the use of board-to-board connectors simplifies the production and testing of electronic devices. In electronics manufacturing, the simplification of testing reflects huge savings on cost. High-density PCBs have more traces and components per unit area. Depending on the investment in the sophistication of a manufacturing plant, a device or product may best be designed with several interconnected boards of medium density than a single high-density board.
Through-hole technology allows a third dimension in interconnecting traces and components on a PCB. The first PCBs may use conductive copper traces in the horizontal and vertical directions along the PCB. By adding more layers of boards, there will virtually be several single-layer PCBs in between the two sides of a double-sided PCB. A typical multi-layer PCB with five layers may be less than 0.08 inches (2 mm) thick. Through-holes have conductive inner surfaces that may carry currents between any two layers of a multi-layer PCB.
Modern electronic devices are more reliable and less expensive to manufacture due to various mature technologies. PCB fabrication for multi-layer boards used to be a big challenge due to the hidden connections between traces of two or more layers of copper. Surface-mount technology (SMT) boosted the miniaturization efforts due to ease of mounting components on PCBs even without drilled holes. In SMT, robotic equipment apply adhesive to component undersides before sticking the component to the PCB. The lead on the pre-tinned leads of the component and the lead on the pre-tinned pads on the PCB will be reflowed or re-molten, and when the PCB is cooled, the soldering process is done.