Wire drawing is a metalworking process that reduces the diameter of a wire by pulling it through a die designed for that purpose. Usually performed at room temperature, wire drawing is different from extrusion in that the wire is pulled through the die, rather than pushed. While the most commonly known application for drawn wire is the cabling used for electrical and communication networks, there are countless other uses as well: paper clips, springs, tire spokes, and musical wire (the wires used in violins, cellos, and other stringed instruments) are all made using drawn wire.
Wire was originally made by hammering metal, such as gold and silver, into very thin sheets and then cutting very thin slices from the sheets. These thin slices would again be hammered into shape until they were fine enough to be used for jewelry or to be woven into clothing. Archaeological evidence suggests that around 400 BC, metal workers were experimenting with wire drawing, fashioning crude dies, and drawing wire through them by hand.

Until the middle of the 19th century, the process of wire drawing became more sophisticated, as craftsmen developed different techniques, including the use of the steam engine to power the actual drawing process. They learned to lubricate the wire being drawn, which decreased the amount of energy necessary to draw wire and marginally improved the quality. However, the quality of drawn wire was always limited by the quality of the metal from which it was made. Metals of inconsistent purity and malleability would routinely break when drawn into wire. Broken wire would need to be spliced, a time-consuming process that resulted in a loss of quality, which was a critical problem for such applications as telegraph communication. The poor quality of the wire drawn increased the time necessary for production and made wire very costly.
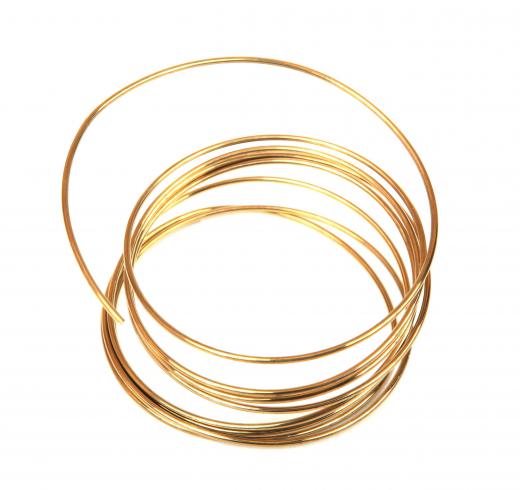
It wasn't until the invention of the Bessemer process in the late 1850s, which produced consistently workable metal, that wire drawing was able to produce wire of a consistently high quality. Metal poured from the converters into molds called billets is cooled only slightly and then the process of forming it into wire in a hot roll mill begins, taking advantage of the residual heat from the Bessemer process. Large coils of thick wire, called wire rod, weighing from 150 to 300 pounds (68 to 136 kilograms), are made in this process.

Once the wire rod has been cleaned of surface impurities, the end is tapered enough that it will fit through the die, which itself is tapered with the opening on one side wide enough to accommodate the wire rod, narrowing up to 40 percent over its length. The tip of the tapered wire rod is grasped firmly and drawn through, reducing its diameter. The narrow wire is usually coiled around a core, although it may sometimes be passed through a smaller die to continue the narrowing process. A thick wire can be reduced in diameter up to 40 percent in a single pass; thinner wire can be reduced by 15 to 25 percent.
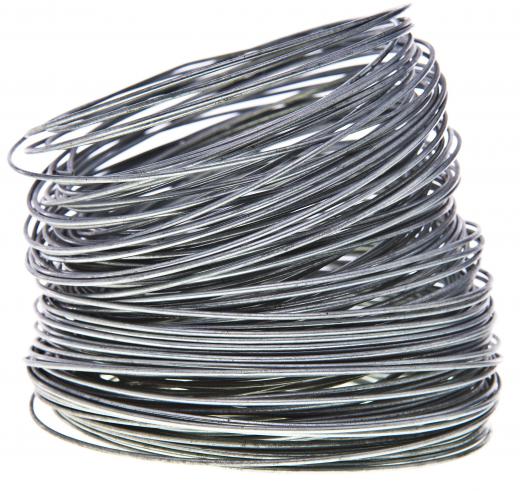
To produce the very fine wires used in telephone cables and stranded electrical cable, wire is drawn through successively narrower dies. Once drawn, wire is sometimes subjected to additional processing, depending on its intended use. For example, a process called annealing, or heating the finished product to a certain temperature for a set period of time, is performed if the wire must be flexible and supple. Thicker wire that will be cut into nails isn't annealed, but will often be galvanized, or coated with zinc, to prevent rust. Wire used in fencing, such as barbed wire, is usually both annealed and galvanized.