Waterjet cutting is an innovative and relatively new technology that allows for precise yet inexpensive cutting of a wide range of materials. The principle behind a waterjet is simple but nonetheless surprising. As the name implies, a jet of water is directed out of an orifice at about three times the speed of sound. The intense pressure of the narrow stream allows the water to actually cut through almost any material placed in front of it.
Although waterjets can cut virtually any material, they are mostly used for flat sheets of plastic, aluminum, steel, tile, and stone. Sometimes an abrasive, such as garnet or sand, is added to the water to improve the cutting efficiency. Some waterjets can cut through 12 inch (15 cm) thick steel!
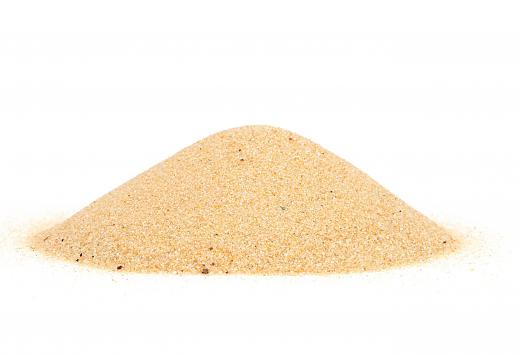
There are many waterjet cutting systems available, but most include a similar set of components. The heart of the system is a pump that increases the pressure of water in a tank up to 4,200 Kg/cm2 (60,000 pounds per square inch). The material to be cut is placed on a large table. A computer-controlled robotic arm or X-Y system controls the stream of water to cut out the desired shapes. The stream of water is very narrow, usually 0.03 inches (0.75 mm), which allows waterjets to cut details impossible to achieve with conventional cutting tools.
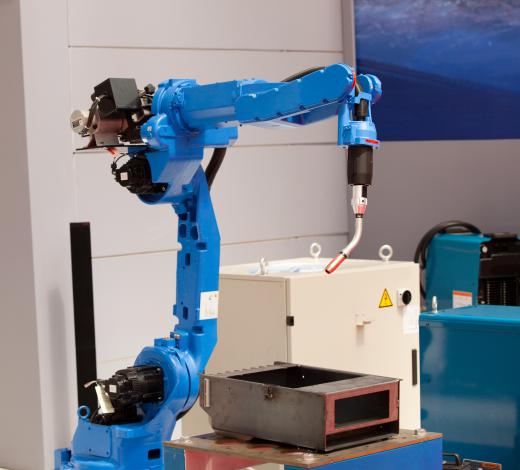
Waterjet systems are usually controlled by a computer so that digital drawings can be used to generate the cutting instructions. Despite the intricacy and accuracy of cuts, waterjet cutting is often more affordable than traditional cutting methods. A further benefit to this type of cutting, is that negligible heat is generated during the process thereby protecting materials sensitive to such stress. One obvious disadvantage, however, is the water itself; wood, paper, and some fabrics are disqualified since they are sensitive to moisture.