Turcite B® is the trade name for polytetrafluoroethylene, a thermoplastic resin used in industrial applications that require the reduction of friction on moving parts and bearings. It is manufactured in sheets, is resistant to chemical corrosion, and is self-lubricating. Common chemical compounds often used to substitute for this product include Delrin AF® and Rulon 142®. Delrin AF® is the trade name for the formaldehyde polymer polyoxymethylene, and Rulon 142®, which has the same chemical make-up as Turcite B®, is prepared as a blue-green solid plastic, with some added metallic compounds such as copper, tin, zinc, and more. Metals such as chromium and bronze can often be added to as fillers as well to increase its strength and thermal properties.
The name is a trademark of the Trelleborg Sealing Solutions company of Fort Wayne, Indiana, a manufacturer of mechanical friction parts, plastics, bearings, and other components designed for reducing friction in various applications. Trelleborg also manufacturers other variations on this resin, including Turcite A®, a plastic designed for heavy loads and which can be easily machined. Another variation is Turcite X®, which is engineered for low load, high-speed applications, making it less wear-resistant than Turcite A® but able to withstand prolonged temperatures of 180°F (82°C).
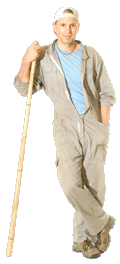
Trelleborg Solutions has had a exclusive partnership since 1995 with a company known as Machine Tool Specialty Components. They apply this product in a friction sealing program known as the Busak Shamblan Turcite B® Slydway® system. Machine Tool Specialty Components is located in Waukesha, Wisconsin, and services manufacturing firms in the U.S., Mexico, and Canada.
The friction solutions provided by the thermoplastic resin operate specifically in a linear dimension. This means that the bearings or slides treated with it are designed to provide free motion in one direction only. Linear motion bearings are often employed in factory settings where roller slides for the movements of products from one station to another are used, and they can either be motorized or non-motorized.
As an industrial thermoplastic, Turcite B® has a tensile strength minimum of 2,000 pounds per square inch (PSI) and an elongation before breaking of 170%. At a hardness level of 50-60, it falls within the soft end of the range for hard thermoplastics. It also shows a greater ability to resist peeling and wear in standardized tests than its main, though less-expensive competitor, Rulon 142®.