Tube beading is the process of crimping to the end of a cylindrical metal tube to form a spout shape. Beaded tube ends are commonly used to connect hoses or slide into other metal tubes. Some tube beading is done simply to strengthen and protect the shape of the rolled metal form. Metalworkers use internal roll forming or ram forming to bend the ends of metal tubes into the bead shape. Many different lengths and diameters of beaded metal tubes are used in the construction, manufacturing and automotive industries.
Manufacturers commonly connect beaded tube ends to create rigid metal forms. Matched tubes are sized to fit inside one another. Connecting tubes are slid together at their beaded ends to form a snug joint. Pressure from the raised lip at the end of the tube holds the joint together. Bolts and welds are often used to fasten beaded tube ends for permanent assembly.
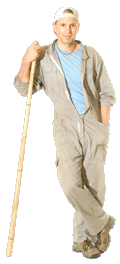
Internal roll forming raises the beaded section by applying pressure from the inside while the tube is held in place. Manual and mechanical devices are used to roll around the diameter of the tube and create the bead in a relatively slow process. The internal roll forming process is typically used for small scale beading and custom tube beading. This method of tube beading is generally considered to be more precise. Some heavy gauge metal tubes will not fit into manual internal roll forming tools.
Ram forming is a faster tube beading procedure that presses internally and externally with a set of punches. Tube ends are formed in a single motion as they are pressed onto the hard metal punches. Large-scale tube beading is done almost exclusively using the ram forming process. The quick ramming process flexes the end of the tube causing the metal to heat up. Beads formed by ramming punches may be slightly uneven or cause minor structural variations in the tube ends.
Either style of tube beading forms a nipple shape at the end of a section of metal tubing that is ideal for connecting to a flexible hose. Hoses attached to beaded ends are often clamped in place. Adjustable screw clamps are commonly used to create an air and watertight seal between the hose and the tube. Adhesives and polymer sealants applied to the beaded ends provide increased protection against leakage. If the tube end becomes damaged, it can usually be bent back into shape to prevent hose splitting.