Tool wear occurs when certain tools that are used for high-impact jobs such as cutting or drilling begin to wear out, changing the cutting profile or the overall effectiveness of that tool. Many different types of tool wear are possible, and the wear will vary according to the type of tool, the type of jobs being done with that tool, and the heat of the tool at the height of its operation. High temperatures often speed up the process of tool wear, especially if the tool is being used improperly or if it is being used very often.
Flank tool wear is perhaps the most common type of tool wear, and it occurs with normal use. It occurs when the part of the tool that comes in contact with the surface being cut or drilled begins to wear down, not necessarily becoming dull but instead becoming weaker. Drill bits and saw blades can incur flank wear after a significant amount of normal use, and enough flank wear will indicate when the tool or part of the tool needs to be replaced.
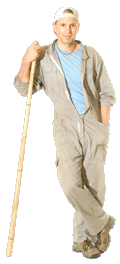
Edge wear is a type of tool wear that occurs on drill bits and can render the drill bit ineffective. It occurs when the cutting edges wear down after high temperatures and high speeds cause the tool to dull on the cutting edge. It occurs most commonly on the tip of the drill bit, but it can also extend down the length of the cutting channels of the drill bit, especially if particularly high speeds are used. This type of tool wear makes the drilling process exceptionally difficult and can even prevent the drill bit from cutting properly. At high speeds, the edge worn drill bit can heat up both the drill bit and the piece being drilled, leading to burning or even breakage of the bit.
Another common type of tool wear is crater wear, in which the cutting edge of any tool becomes pitted, or chips of metal are broken from the cutting surface. While this type of wear can cause the cutting process to change slightly, it is not usually a significant problem unless the drill bit or other cutting tool begins to cut too much or not enough material, thereby altering the cutting shape or efficiency. Build-up tool wear can also occur; this happens when material on the cutting surface heats and then transforms, building up into an altered cutting surface. This happens most often at high speeds and high heat, and it can alter the cutting process significantly.
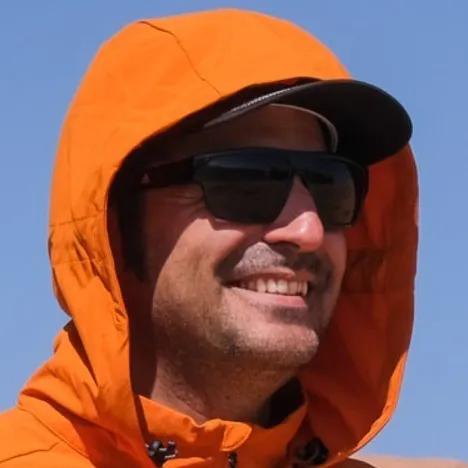