Thermal depolymerization is an industrial process for breaking down various waste materials into crude oil products. This involves subjecting the materials to high temperatures and pressure in the presence of water, thereby initiating a process known as hydrous pyrolysis. The result is the depolymerization of the materials' long chain polymers into short chain monomers, in this case petroleum hydrocarbons. This is a greatly accelerated artificial rendering of the process that formed fossil fuels in nature. A wide range of waste products, known as feedstocks, may be used in thermal depolymerization processes including plastics and biomass materials.
The thermal depolymerization process (TDP) has been in existence for approximately 70 years but was not considered viable until the late 1990s. This lack of viability was a result of unacceptable energy returned on the energy invested (EROEI) rating, i.e., the measurement of the amount of energy taken to produce the energy output. Early methods required far more energy to produce than the energy output but paved the way for modern systems which feature EROEI ratings of 6.67, or approximately 85 units of energy produced for each 15 expended. Conventional agricultural production of biodiesel and ethanol feature ratings of about 4.2, thereby making the thermal depolymerization process an attractive option. Apart from its efficiency, the system has several other benefits including breaking down heavy metal contamination into harmless oxides and the destruction of organic poisons and the prions responsible for mad cow and Creutzfeldt-Jakob diseases.
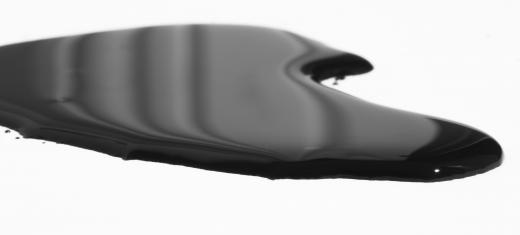
In practice, the hydrous pyrolysis process at the heart of thermal depolymerization is fairly simple. Feedstock materials are first ground into small pieces and mixed with water. The mixture is then heated to 482°F (250°C) for approximately 15 minutes in a pressure vessel. The steam generated raises the pressure in the vessel to approximately 600 pounds per square inch (PSI) which, at the end of the heating process, is rapidly released. This causes the water to flash off or rapidly evaporate, thus leaving residual solids and crude hydrocarbons behind.
These constituents are separated and the hydrocarbons collected for further refinement. This involves further thermal treatment to 930°F (500°C) and fractional distillation sorting. The results are light and heavy naphthas, kerosene, and gas oil fractions which are suitable for the production of several grades of fuel oil. The residual solids remaining after the initial thermal treatment may be used as fertilizers, filters, soil fuels, and activated carbon for wastewater treatment.
The list of TDP suitable feedstocks is extensive and includes waste plastic, tires, wood pulp, medical waste, and rather unsavory byproducts such as turkey offal and sewerage sludge. The efficiency of the thermal depolymerization process is further enhanced by the fact that process byproducts such as methane, which can't be broken down by depolymerization, are collected and used to power turbine generators to produce electricity for the facility or resale. Methane also possesses potential as biogas, a green alternative to conventional gasoline.