The process of spark testing typically involves using one of two different methods to generate sparks from an iron alloy. These sparks can often be used to identify the type of ferrous metal that the object consists of. A person with a well trained eye may be able to identify the general alloy through simple observation, or some type of chart may be used. There is also a process known as automatic spark testing, which can use spectroscopy and certain other methods to remove the possibility of human error. In cases where a positive identification of the metal in question is necessary, a process like chemical analysis may be used instead of spark testing.
There are two main methods of generating sparks to test. The first involves a grinding wheel, which the object can be placed against. This wheel will often be made of carborundum or aluminum oxide, which can abrade and heat small pieces of metal into bright sparks. The other method is to heat the sample with a torch or other apparatus until it is red hot. Compressed air can be blown on it, which will cause the metal to ignite and send off a uniform shower of sparks.
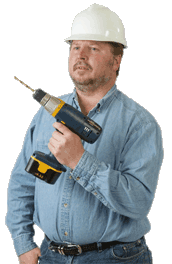
Each of the different ferrous alloys tends to have its own unique spark pattern. Some metals create a longer stream of sparks, while others may have sparks of different lengths. A practiced eye may be able to tell the difference in these spark patterns, or comparisons may be made to either known samples or photographs. Automatic spark testing can also remove the human element by using methods such as spectroscopy and spectrometry to observe and classify the pattern.
There are a number of benefits to spark testing. The process is typically very quick, requires no specialized equipment, and can therefore be inexpensive when compared to other methods. A potential downside is that the process can damage the sample, as the sparks consist of abraded pieces of the metal. Scrap is usually used for this reason so as not to damage a piece that will later be used for another purpose.
In addition to its use in determining the specific classification of a ferrous metal, the process can also be useful in sorting samples by type. Rather than comparing the sparks of one piece of metal to a known sample or photograph, this process can simply involve comparing pieces to each other. If the sparks are identical, then the objects are probably made of the same alloy, and those with differing spark patterns can be sorted into separate groups.