Resistance heating is a process where thermal energy is produced by passing an electrical current through a purpose designed conductor. The resistance the conductor offers to the passage of the current causes a reaction within it at an atomic level, thereby producing energy and releasing heat. This reaction is subject to a scientific relationship known as Joule's first law which sees the amount of heat generated by the process dependent on the balance between conductor resistance and current magnitude. Resistance heating is one of the most commonly used forms of heat generation and is found in a wide range of domestic and industrial applications. Resistance heating is a product of all circuits where electric current encounters resistance; although it has many beneficial uses, it can damage or destroy electrical equipment if not controlled.
Anyone who has used a kettle, toaster, or a bar heater on a chilly evening has made the acquaintance of resistance heating. The effects of resistance heating were first noted in the mid-1800s by James Prescott Joule and the phenomenon quickly became the cornerstone of one of the most widely used forms of heating of all time. The basic principle of resistance heaters centers around the reaction caused when the electric current electron flow encounters the ion structure of the conductor. The electron/ion collisions which result see a portion of the energy of accelerated electrons released in the form of thermal energy. If the current flow or the resistance of the conductor is increased, so too will the amount of heat generated.
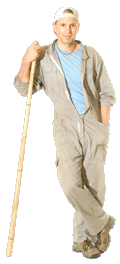
Resistances heaters most commonly take the form of a coil or helix or specially designed resistive wire embedded in or wound onto a heat resistant, insulating substrate. Most resistance heating elements are of this type with materials such as high-alumina ceramics being the most common insulators. The most common metal combination in the manufacture of the wire used in resistance heating is an alloy of nickel and chrome. The average composition of these alloys runs between 60/16% respectively for general uses and 80/20% for high end conductors. The nickel chrome 60 alloy is the most widely used of the two and can withstand temperatures of 1850°F (1000°C) without sagging or deforming.
Although resistance heating is obviously beneficial, the phenomenon can have catastrophic effects when uncontrolled. All electrical conductors generate heat to a certain degree; when circuits or equipment become overloaded, the heat generated can severely damage or even destroy an appliance. Electrical fires are also a common result of uncontrolled resistance heating.