Prestressed concrete is a combination of high strength concrete and steel strands. This combination makes a very strong structural material that is used in the building of roof slabs, bridge girders and railroad ties. Prestressed concrete was invented and patented in 1886 by Henry Jackson, a San Francisco engineer. This type of concrete became the material of choice in Europe after World War II, due to the shortage of steel. The Walnut Lane Memorial Bridge, built in 1951 in Philadelphia, Pennsylvania, became the first structure in America made of this type of material.
An ordinary concrete beam, even without a load, struggles to carry its own weight. When service loads are added to the weight of the beam, it develops hairline cracks. As time passes, these cracks will get larger and eventually the concrete will crumble. Thin concrete pads tend to bow when additional weight is added, resulting in the shifting of the home. These changes are why prestressed concrete was invented.
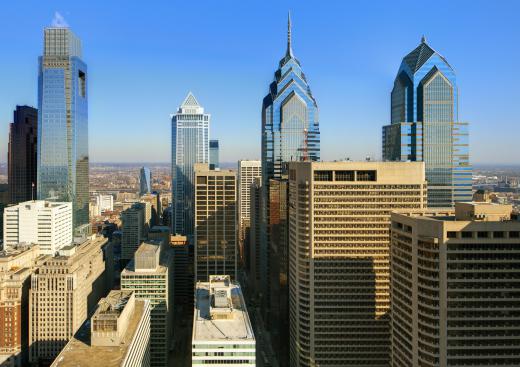
Prestressed concrete can be created using two different methods; pre-tension and post-tension. The pretension method involves stretching high tensile steel strands between abutments located at both ends of the concrete casting bed. After the strands are taught, concrete is poured into the beds, where it surrounds and adheres to the strands. Once the concrete is dry it will have bonded to the steel. After the concrete has reached the desired strength the strands are released, resulting in the concrete developing a slight arch that makes it more resistant to heavy loads.
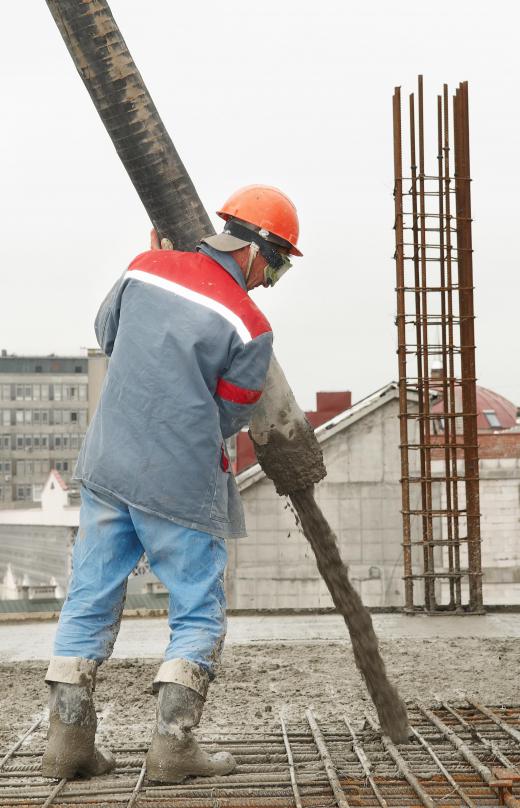
There are several reasons to use this type of concrete in various structures. Beams are made of prestressed concrete so they can resist stress without cracking. A pile is prestressed so it doesn't crumble with the forces of heavy transportation and driving. Columns are made of prestressed concrete so they don't buckle under the weight of heavy loads. Thin concrete pads are prestressed to keep them from bowing under normal weight.
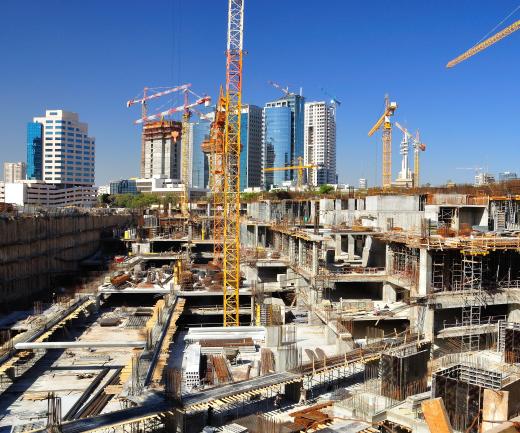
Creating prestressed concrete using the post-tension method involves applying compression after the concrete has been poured and hardened. The concrete is poured around a curved duct that has had steel strands ran through it. Upon curing, tension is applied to the strands using hydraulic jacks. The strands are then wedged into place so the tension remains after the hydraulic jacks have been removed.
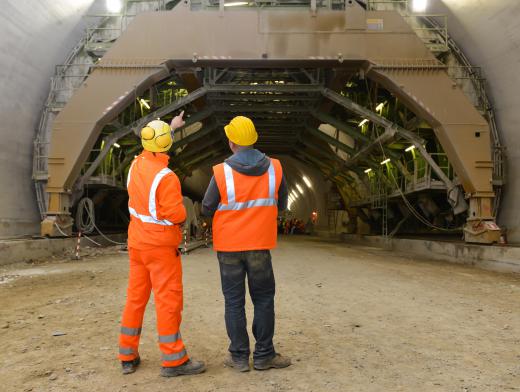
Concrete created via the post-tension method is used as monolithic slabs for houses located in areas with expansive soils such as adobe clay. This type of concrete is also used for creating structures where seasonal expansion and contraction of the soil is an issue. Post-tensioned concrete is highly efficient for constructing buildings with more elaborate designwork.