Panelized construction is a method of building certain parts of a house in a factory rather than onsite. This construction method is the natural midpoint between a standard stick-built home and a completely modular premanufactured home. Panelized construction eliminates a lot of the time and waste associated with traditionally-built homes, but allows for variation in construction and design, something unavailable with premanufactured homes. It isn’t uncommon for homebuilders to use some panelized parts when building a home, even if they say it is hand-built.
A housing panel is a framework of a wall or roof that was assembled in a factory rather than onsite. These premade sections save time and money when putting together a house. Since these pieces are always nearly identical, the actual construction of a panel can take place elsewhere, and it will be nearly indistinguishable from one built locally. The builder may make small modifications after the panels arrive to customize them to a specific project.
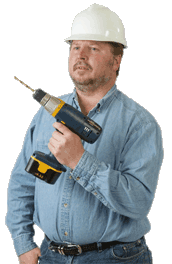
There are many advantages and disadvantages to panelized construction. The majority of the pluses relate to time and money, while the majority of the minuses relate to the panel company. In either case, they have certain additional advantages and disadvantages when compared to a stick-built or premanufactured home.
The two primary advantages are time and money. Panelized construction allows the framing phase of the house to move by very quickly. This reduces the time the builders spend on the house and the money the homeowner needs to pay.
The disadvantages to panelized construction include the panels costing a lot to ship. This may end up making them more expensive than if the builder had made them himself. In this case, there is still a time savings, but less of a money one.
The other major drawback is in quality control. Some companies are much more careful in their construction than others. If a panel is assembled poorly, the turn around on shipping it back and getting a replacement may eat up the time savings gained by using panels.
When compared to other building methods, there are even more things to consider. A stick-built home gives the most freedom in design and flow. With a panelized home, the panels come in a variety of configurations, but only common sizes. This reduces the freedom of design, but also reduces build time and cost. A premanufactured home is livable in just a few days, but the homeowner has no say in its overall configuration—these homes will typically cost the least, but they have little variety.
Are Panelized Homes Cheaper?
Construction costs for new homes vary across the country. Certain situations can cause more expense, but building costs for a stick-built home is usually between $100 and $200 per square foot. Panelized homes generally save 10 to 25% off those costs.
Using pre-built panels in construction means that laborers don’t have to be as skilled as those that build traditional houses. Less skill equals less pay, which is one way that panelized construction saves money.
Most floor plans use many sections of walls and roofing that are identical. While some walls include doors or windows, many are just plain walls with no differences.
Walls
To stick build a wall on-site, carpenters must carefully measure the distance between studs. Headers and footers are attached, then the wall is raised into place. When panels are used, they are just brought to the appropriate position and secured into place.
Bringing a panel to the correct spot is much faster than having to bring the individual pieces of wood to the spot, measure the spacing and secure them to the headers and footers. Less time spent working means that contractors don’t have to pay for as many man-hours.
Lumber prices can be very expensive if it’s bought in smaller quantities. Panel manufacturers use larger quantities than an average contractor, giving them buying power to get their lumber at better prices.
Traditional homes usually take up to four months more construction time than those that use panels. This fact saves both time and money. This shorter build time is particularly beneficial in regions where the climate shortens construction seasons.
You can use panels that are built to include only the framing and exterior sheathing, or you can choose panels that include rough-in components and exterior finishes.
Roofs
Stick-building a roof is very time-consuming. Notches must be cut into every rafter at the appropriate angle and place. The ends of the rafters where they attach to the ridge board also need to be cut at an angle. Collar beams have to be added once the rafters are secured to the house frame to provide stability.
Pre-made roofing trusses are much easier to install than using traditional framing methods. In addition, truss support systems provide extra stability to the roof.
Even for roof designs that require dormers or other odd shapes, using trusses for the main part of a roof saves time and expense.
Building Process
Stick-built walls and roofs are constructed entirely on-site. There is a greater potential for waste due to incorrectly measured pieces of lumber and worker error as opposed to using panels.
Panels are built in a factory using technology and a production line. This process allows for more consistency and less waste.
What Are the Disadvantages of Panelized Construction?
While panels and trusses can save both time and money, using them does have some disadvantages.
Transportation Costs
Wall panels and trusses are large, awkward and heavy. They have to be transported from the factory to the construction site using a flatbed semi-truck, and must usually be unloaded on-site using a forklift or small crane.
Semi-truck companies charge by the mile. Depending on the distance between the manufacturing facility and building site, the cost of transportation can get expensive. That can cut into the amount of money saved by using the panels. If contractors need to rent heavy equipment to unload the panels, that’s another expense deducted from the overall savings.
Quality Control
Some companies that manufacture panels use quality lumber and exact specifications when building the panels. However, not all do.
If inferior or defective panels arrive at your construction site, you will either have to return them to the manufacturer and wait for replacements or take the time and materials to repair them. Both scenarios require extra expense and cause construction delays.
Lack of Flexibility
When using traditional framing methods, contractors can make modifications to the blueprint during construction rather easily. However, once wall panels are ordered, potential design changes to the on-site building are limited. Contractors can make minor modifications to pre-built panels, but extensive alterations aren’t possible.
Is a Panelized Home Right for You?
There isn’t a definitive answer to that question. If you are building a custom home, panels don’t necessarily work well. If the distance between your construction site and the panel factory is extensive, the shipping costs might be prohibitive. If you want the ability to modify your home design as you go, using wall panels probably isn’t the best choice.
If you have a relatively consistent floorplan and access to a reasonably close-by panel manufacturer that is known for producing quality products, panels may save time and money.
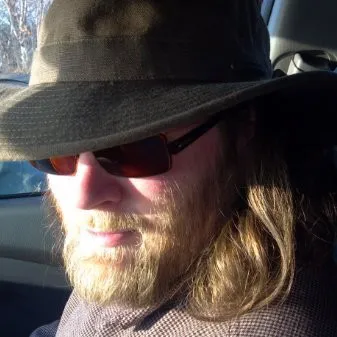