Package testing evaluates the suitability of cushioning or bracing material surrounding products prepared for shipping to customers. These tests send merchandise through a series of experiments to determine if packaging materials protect contents from damage or breakage. Package testing can be performed on individual boxes or an entire shipping container to measure unit loads and movement during transport.
Manufacturers of all types of products benefit from package testing to reduce waste from damaged merchandise returned by customers. They might be able to curtail packaging costs if testing shows less foam or cushioning material is needed to ensure safe delivery. When less packing material is used, it reduces waste in landfills, decreases the amount of storage space needed in warehouses, and requires fewer trucks to transport finished products.
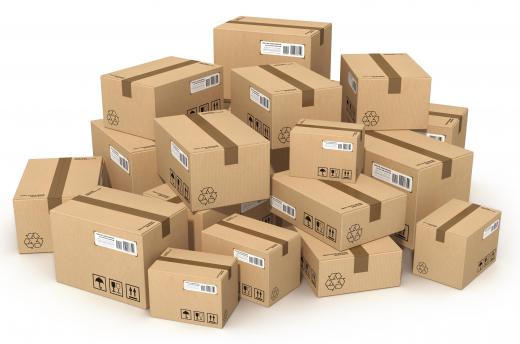
Companies outfitted with chambers and equipment capable of performing a number of experiments usually perform package testing. Environmental chambers evaluate how packaging materials hold up under excess humidity, extreme temperature fluctuations, and altitude variations. Packages exposed to these conditions are later opened to analyze any damage to the contents or shipping container.
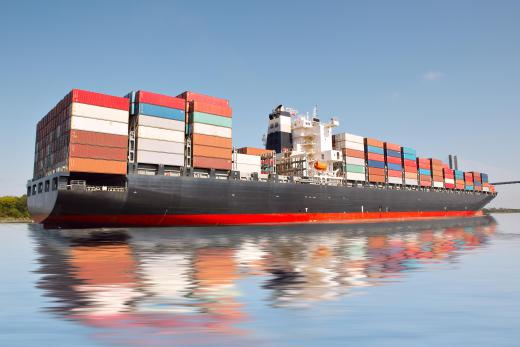
One common test measures how vibration and shock affect goods. It might include dropping boxed merchandise from an elevated platform to measure the degree of breakage or damage to outer packing materials. Vibration package testing simulates jostling that might occur as the merchandise is transported by truck, over railways, or by ship. It analyzes whether items inside a box or carton shift when bounced or shaken.
Packing testing might also evaluate the force needed to insert stock into shipping containers, and how easily it can be removed. If too much pressure is required to pack or unpack goods, it might damage sensitive or fragile parts of a product. Along with determining packing and unpacking ease, package testing typically determines which type of material best protects the product.
In certain industries, package testing might serve as a critical component of manufacturing. Medical devices might represent especially sensitive equipment that is easily damaged. Maintaining sterility defines another need when shipping medical equipment. Packing testing exposes seals on sterile products to various temperatures, altitudes, and humidity levels and determines if the seals leak.
Companies that ship hazardous materials typically must meet packing regulations set by agencies that govern safety of these products. Package testing for chemicals and other hazardous substances protects employees, transport workers, customers, and the public from dangerous spills. Tests on these goods typically involve extreme shock that might occur when trains employ switching devices, and the force that might occur in an accident.