Lost-foam casting (LFC) is a casting method used to create solid metal parts from molten metal. When a part is created through casting, a mold is used to produce the desired shape. In lost-foam casting, the mold is made from polystyrene foam, which is lost during the casting process as the liquid metal melts it and replaces its shape — hence the name “lost-foam.” Although lost-foam casting is often used to make machine parts, decorative and other objects can be produced using the same method. The tools used by casters range from homemade devices to industrial-grade equipment.
The first step of lost-foam casting is the creation of the foam mold. A block of polystyrene foam is cut into the exact shape of the finished product using hand or power tools. For applications where the dimensions of the finished piece must be exact, power tooling is preferred for a more consistent shaping of the foam. The mold is then dipped in sheetrock mud or plaster and coated thoroughly.
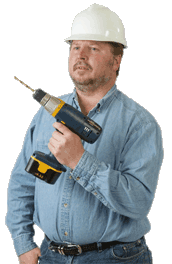
After the foam mold is finished, it is buried in a container — for example, a metal drum — filled with compacted sand. The very ends of the foam shape are left exposed to facilitate the entry of the molten metal into the mold. A homemade tool can be used during this step to help the process along further. This tool, which consists of a hinged cylinder that can be opened and closed along the side by long handles, is placed on the sand so that it surrounds the foam piece. When the metal is poured, the cylinder walls contain it and allow it to build up over the piece, creating more pressure and, therefore, a more thorough casting.
Aluminum is often used in lost-foam casting, especially by hobbyists, but it is possible to use any metal as long as it is hot enough to evaporate the foam mold. In most cases, the molten metal must be at a temperature of 1000° F (about 538° C) or higher. Furnaces capable of melting metal at these high temperatures can be purchased commercially or made from everyday materials such as clay or brick. The metal is melted inside a special container known as a crucible, which is made from a material with a high melting point, such as graphite. Once the metal is melted, the crucible is gripped using tongs or fixed bars and tipped to pour the liquid metal onto the mold.
As the molten metal dissolves the foam, it flows into the empty area and assumes its shape inside the sand. Ideally, a perfect replica of the foam piece is created in this way. The piece is allowed to cool for a few minutes, and is then removed from the sand for further cooling in a bucket of water. After sand and debris are brushed from the piece, it can be polished or machined further as needed.