Induction welding is a method of welding often used to join thermoplastics. It uses a power supply and heating coil to melt a small amount of joining compound at the joint between two pieces of plastic. A typical weld takes just seconds to complete, results in strong joints, and does not distort the material being joined.
Thermoplastics are plastics made from polymer resins. When cool, they are solid, but they melt easily when heat is applied. Celluloid, acrylic, and polyurethane are all common types of thermoplastics. They are used to make everything from bird feeders to car parts.
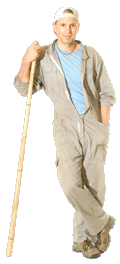
An operator begins the process of induction welding by placing a small amount of thermoplastic compound in the joint between the two pieces to be welded. This compound can take the form of tape or wire or be molded as a gasket. It is either made from the same polymer as the pieces to be joined or from a compatible polymer.
The compound contains a magnetic powder at a concentration of about 15 percent by volume. This powder is usually iron, iron oxide, or stainless steel, and it is used to facilitate heating of the compound. The faster the compound heats, the faster the weld is completed.
The heat is provided by an induction coil attached to a high-frequency power supply like a radio frequency generator. When the generator is switched on, alternating current (AC) power passes through the coil. This produces eddy currents, which heat the magnetic powder. When the surrounding thermoplastic compound gets warm enough, it softens and melts. At this point, slight pressure applied to the pieces to be joined will result in a joint being formed.
Induction welding has several advantages over other methods of joining pieces. First, it is fast. The thermoplastic compound melts in a matter of seconds when heated and cools almost instantly when the current is turned off, forming a solid joint almost instantly. Second, induction welding does not distort the materials being welded. As the heat is aimed at the compound rather than the parts being joined, the parts are less likely to suffer stress caused by heat.
Finally, the use of a thermoplastic compound results in strong joints. The compound completely fills any gaps between the two pieces being joined, preventing weak spots. Also, because the compound completely melts and re-solidifies, it actually forms a molecular bond with the materials being joined. This results in a joint almost as strong as the material itself.