Heat setting is a textile industry process for removing spinning- and cabling-induced torque and impart dimensional stability in fibers and yarns. The process may also cause synthetic fibers to gain bulk or volume and is also used to stabilize fibers after processes such as friezing. Heat setting is a thermal process which utilizes either steam or a dry convection heat source to set the fabric or yarn. This process is typically carried out in an enclosed pressure chamber or autoclave or on open conveyors exposed to steam sprays. Steamsetting is a standard post-production process for a wide selection of natural and synthetic fibers intended for the garment and carpet industries.
When fibers are spun, tufted, or woven into workable yarns, the process induces a torque reaction which can cause kinking or twisting of the finished product. To neutralize these torque effects, manufacturers expose the yarn to a process known as heat setting or thermal fixing. During this process, the fibers are exposed to a wet or dry heat source which reduces the induced torque by a combination of thermal expansion and chemical or molecular reactions to the heat and moisture. The process can also cause synthetic fibers to gain volume in a reaction known as bulk development. Heat setting is also extensively used to stabilize carpet fibers after they have been subjected to frieze processing.
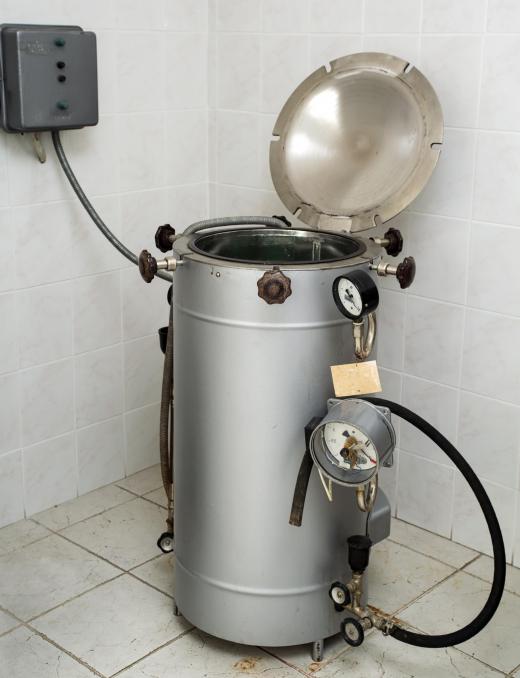
The process of heat setting involves exposing yarns and fabrics to wet or dry heat in the form of superheated steam sprays or hot air convection. One of the older methods of heat setting fabrics is the autoclave which, although still in use, is being replaced by more efficient methods with higher turnover rates. An autoclave is an enclosed vessel that heats its contents under high pressure or deep vacuuming. The fabrics or yarn are loaded into the autoclave in skeins, on bobbins, or in a separate container and heated to stabilize the fibers. Although effective, the autoclave method is slow, labor intensive, and does not lend itself to integration into a seamless production process.
Newer heat setting processes such as the Resch Steamatic in-line steamer, power-heat, and TVP systems allow for easy integration into production lines and typically involve passing the freshly spun fiber through the heating stage on a conveyor. The Steamatic system places the heat setting phase between the ring spinning and winding stages where the fiber is steamed in a vacuum and dried. The power-heat-set method was the first continuous process developed and involves subjecting the fabric to a superheated steam and air spray at atmospheric pressure while on the process conveyor. The TVP system transports yarn and fabric through a pressure tunnel on a conveyor where it is heat set with saturated steam. The stabilized yarn is then moved onto the winding stage after it has cooled.