Finite element analysis, or FEA, is a computer-based tool for approximating the solution to an otherwise unsolvable problem. It is commonly employed in structural engineering, though it is also used in other problems like fluid mechanics and heat flow. Most mathematical problems for practical applications are, in fact, too complicated to be solved analytically, though in most cases, they do not require perfect solutions. Finite element analysis is a numerical—as opposed to an analytical—technique for obtaining acceptably accurate solutions; it works by breaking a complicated problem into many simpler ones.
Analytical methods involve solving a mathematical problem to give a perfect, continuous solution. In other words, the solution is a function in terms of some variable, rather than a numerical approximation. There is no degree of estimation or error in analytical solutions to a given equation. There are often no known analytical solutions to formulations that model real-world problems, however. These require numerical methods, of which finite element analysis is one example, to obtain an approximate solution.
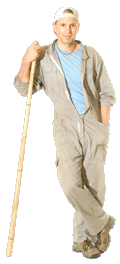
Finite element analysis relies on breaking a complicated problem into a large number of less complex problems. When the solution to a problem exhibits very complicated behavior, it is sometimes acceptable to apply simplifications. Often times, though, a broad simplification introduces too much error to be useful. This is when breaking up the problem into many separate problems can help. Simplified solutions to each element of a problem can be integrated together to give a highly accurate general solution.
In finite element analysis, the domain of a problem is broken into many smaller zones called elements. The collective body of elements is called a mesh. The process of integrating, or summing up, many different elements works because of the way elements interact at their boundaries. When the boundary interactions of elements are understood, a computer can extend the approximate solution from one element to the next. In the end, the computer will have “built” an approximate solution that is very close to real-world behavior.
One problem commonly solved with finite element analysis is the distribution of stresses within a solid piece of metal. When metal, or any comparable material, is subjected to forces, each part of the object has a certain stress on it. Even if the applied forces are known, irregularly shaped objects are typically too complex to know the exact distribution of internal stresses. At this point, finite element analysis can be used to calculate an approximate solution—element by element—to this problem. Visualization software can then be used to put this collection of information into an intuitive and coherent picture.