Electrospinning in an industrial process in which a high voltage electrical charge is used to create polymer filament fibers. The process differs from electrospraying, which uses droplets, in that the electrically charged liquid polymer is pulled in a solid strand. There are two methods used to create the liquid polymer used in electrospinning. It can be melted from its solid form, or it can be mixed with a solvent to form a polymer solution.
In the laboratory setting, basic electrospinning equipment can be set up using a high voltage power supply, a glass pipette, a syringe, and a metering pump to deliver the electrically charged liquid. The other component of the setup, the capillary screen, is connected to the electrical ground. This screen may be stationary or it may rotate to facilitate spinning of the fibers. Using this simple setup, researchers in the field of nanotechnology have created polymer filaments and nano-woven materials, which are used in medical and industrial applications.
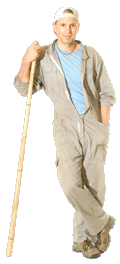
The methods used for electrospinning are quite basic. The liquid polymer is electrically charged by means of a wire electrode immersed in the liquid. It is then pressurized, forcing it to move towards the end of a glass tube. As the liquid polymer reaches the end of the tube, the electrically charged ions of the fluid become attracted to the oppositely charged capillary screen. As the surface tension of the liquid is overcome by the drawing force of the capillary screen, it forms a cone shape, called a Taylor cone.
The surface tension becomes completely overcome at this point by the pull of the electrically charged capillary screen, and thin threads of liquid polymer begin to form. As these threads stretch out, they grow longer and thinner in a process called whipping, which resembles the movement of an electric arc through air. The filaments are carried through the air and are eventually collected on the capillary screen.
The fine filaments created during the process of electrospinning can be just a few nanometers in diameter. These threads may also display unique textures and surface qualities, which make them desirable for a variety of applications. In the medical field, nano-woven fabrics are used to make wound dressings, frameworks for artificial organs, and drug delivery patches. Research laboratories also use these fabrics to make filters that can isolate sub-micron particles. Industrial applications of the electrospinning process are also being discovered, offering such options as seamless clothing or composite building materials.