Electrochemical machining (ECM) is a metal machining process involving the removal of material from a workpiece by means of electrochemical erosion. This process is achieved by passing a high current electrical charge from the positively charged workpiece through an electrolyte solution to the negatively charged “cutting tool.” This causes molecules from the workpiece to dislodge into the electrolyte in a profile that mimics the shape of the cutting tool. In this fashion, a “cut” is made in the workpiece of the same shape as the cutting tool. Although limited to use on electrically conductive materials, electrochemical machining offers several benefits including the cutting of complex internal profiles and minimal stress transfer to the workpiece.
Potential uses of electrochemical machining were already the subject of interest and experimentation as far back as the 1930s and have been a commercial reality since 1959. The principle which underpins the process is the same as electrolysis for electroplating. In ECM applications, however, the process is reversed; material is removed from and not deposited onto the workpiece. This is achieved by placing a specially shaped cathode in close proximity to, but not touching, the workpiece. A pressurized electrolyte solution is pumped between the two and acts as a conductor for a high current charge which passes from the workpiece to the cathode.
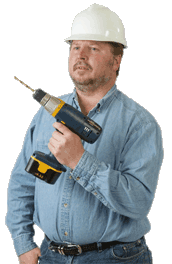
This current flow causes the workpiece to erode at a molecular level to form a cut which follows the shape of the cathode. This means that the cathode effectively becomes the process cutting tool. The material that dislodges from the workpiece is carried away with the electrolyte, thereby subjecting the cutting tool to very little wear during machining. The gap between the work piece and cutting tool during machining is maintained at between 0.003 and 0.03 inches (0.08 mm and 0.8 mm).
This lack of physical contact between the cutting tool and workpiece is one of the electrochemical machining method's greatest advantages because no stress or heat is transferred to the workpiece during machining. It is also possible to machine very hard materials without the related costs of expensive, ultra hard tools. Electrochemical machining is thus an appropriate way to produce very hard, precision parts such as turbine blades. A wide range of complex profiles, both internal and external, may also be machined using the procedure. The only real disadvantages of ECM techniques are the high initial installation costs and the corrosion risk to tools and workpieces posed by the electrolyte solution.