Dip molding is a manufacturing process in which a heated mold is lowered into a liquid polymer bath to attract a layer of coating which can be cured and peeled off for a finished part. The properties of the plastisol, the polymer bath, can be varied in order to produce different kinds of components, ranging from beverage insulators to surgical gloves. It is also possible to use the same process for dip coating, in which case the object to be coated is heated and lowered to allow the plastisol to adhere directly; this can be seen with things like tools with easy-grip handles.
The plastisol bath contains particles of Polyvinyl Chloride (PVC) suspended in a material known as a plasticizer so it will be liquid at room temperature. Heat from the mold attracts the plastic and encourages it to start setting. High heat attracts a thicker layer, as does a longer dip, which allows more plastic to build up during the dip molding process. By controlling heat and length of dip, the company can determine the thickness of the coating.
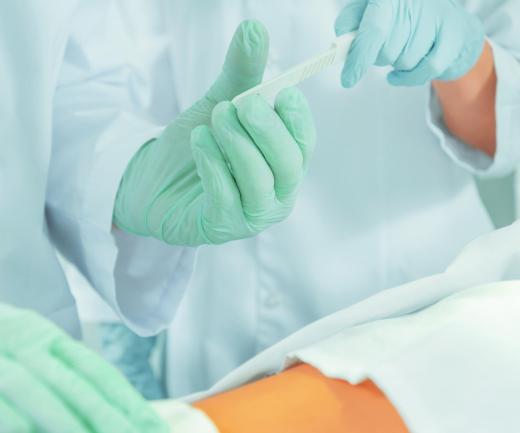
Early dip molding techniques primarily resulted in hard, shiny coatings. Changes in the technology have allowed for a range of textures and appearances for different applications. These include plastics that can perform in different environments, like extreme heat and cold. The process can even produce plastics that behave like more expensive rubber coatings, allowing companies to manufacture components like tools with handles that feel rubberized.
Multiple dip molding steps can be used if a company needs a product with several layers. Thermal insulation, for example, can include several layers and an outer coating to control the finished texture. Increased flexibility with the process makes it more applicable to a wider range of manufacturing processes. Companies that produce dip-molded components can also work on custom projects by request from clients, including specialized molds and plastics for particular applications.
Molds used in this process are known as mandrels. They can be generic for the production of items like surgical gloves or foam insulators, or they can be customized for specific projects where a particular shape is needed. Custom creations can be expensive, but may be maintained in a company library for use in future dip molding orders from that client. These can be less expensive, because the manufacturer already has the mandrel and just needs to be prepare the plastisol bath to produce the desired part for the customer.
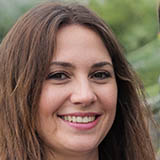
Ever since she began contributing to the site several years ago, Mary has embraced the exciting challenge of being a About Mechanics researcher and writer. Mary has a liberal arts degree from Goddard College and spends her free time reading, cooking, and exploring the great outdoors.