Diamond turning involves the use of diamond-tipped lathes or other machine tools to create precision elements. Several lathes are used which are controlled by computers and with the machine parts placed on a granite base. Diamond-tipped tools cannot be used on metals like steel, and regular inspections are necessary during the cutting process to ensure accuracy. The precise nature of diamond turning is its biggest problem because a high percentage of defective parts are created.
Diamond turning creates aspheric optical elements from materials such as metal and crystal. This results in products such as telescopes, scientific research instruments, and missile guidance systems. The majority of diamond turning is performed by tools such as lathes which are controlled by computers.
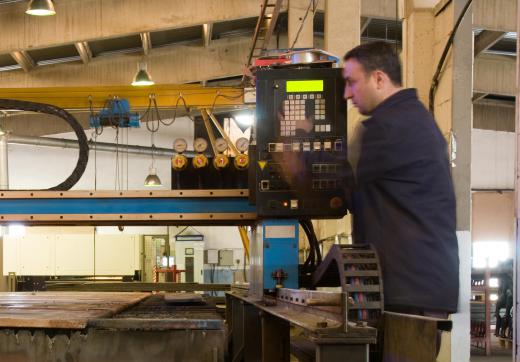
There are several different stages in the diamond turning process. Usually, several CNC lathes are part of the process, each more accurate than the last. The final stage of this process involves a lathe that is diamond tipped to ensure a high level of accuracy. Each stage is monitored by laser equipment and electron microscopes.
The diamond turning lathe is placed on a granite base which has an incredibly accurate surface finish. This base is then placed on top of air suspension which makes sure the work surface stays horizontal. The machine parts are put on the granite base with hydraulic suspension to ensure accuracy. Negative air pressure connects the machined element to an air chuck. Another air suspension ensures that the chuck is kept away from the electric motor which causes it to spin.
Electric motors are used to move the cutting tool. A computer controls the tool’s coordinates. The depth of the cutting passes increase until the final surface is completed.

It is only possible to use diamond turning on certain materials. This includes plastics such as nylon, metals like copper, and infrared crystals such as silicon. This process cannot be performed on steel or iron,however, because the carbon in the tool reacts poorly with materials, thereby causing damage and dulling the tool.
Although it seems like the whole process is computer operated, a manual operator is still important. Maintaining the highest quality is the chief purpose of this method which is why there must be checks carried out at the end of each cut. All it takes is one miniscule error for the part created to become defective.
One major problem with diamond turning is the high level of faulty parts that are produced. This means that manufacturing costs are exceedingly high as compared to other methods of polishing. There is a lot of manual labor involved in the process which does not produce as many parts as other methods.