Deburring is, to put it simply, a finishing method used in industrial settings and manufacturing environments. Metal is frequently machined using many processes in order to create pieces of specific shape and size, and it may be welded, molded, cast, trimmed, slit or sheared. These procedures often create ragged edges or protrusions. The raised particles and shavings that appear when metal blanks are machined are referred to as burrs, and the process by which they are removed is known as deburring.
There are several methods that can be used to remove burrs. Abrasive substances may be applied, or abrasive cloths may be used to rub the metal in order to remove thin shavings and small notches, as well as to polish the piece. In other cases, sanding may be necessary, whether this means a small amount of sanding by hand or rigorous sanding with a machine for more troublesome deformities.
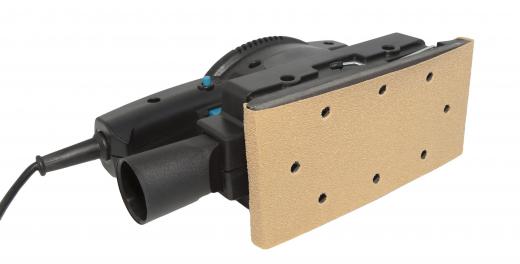
Other methods require repetitive filing or use of a grinder to smooth away nicks and fragments. Deburring and polishing may be necessary for more than one section of a metal component, since burrs and shavings can occur on seams as well as edges. All surfaces need to be completely smooth.
Deburring is important for quality, aesthetics, functionality, and the smooth operation of working parts. It is also important for safety, since even a small notch can cause moving parts to catch, creating the potential for accident, injury, or unnecessary delay in production. Rough edges can also cause injury when individuals are required to handle blanks. Each of these preventable problems can cost companies a great deal of money.
It's also necessary to remove burrs in woodworking. When pieces of wood are cut, ripped, or shorn, wood blanks can also develop rough areas, often in the form of shavings, chips or splinters. With wood, the most common methods of smoothing the piece are sanding and filing. Sanding may be accomplished with a power sander, or simply by touching up the worst spots by hand. Edges may also be finished with a router.
Deburring greatly improves the quality and functionality of metal and wood pieces, making it a necessary use of time and a cost effective process.