DC (direct current) sputtering is a material deposition process used to coat substrate structures with thin films of different materials. The process involves bombarding a donor material with ionized gas molecules, causing a displacement of donor atoms. These atoms then adhere to a negatively charged recipient material creating a thin film on its surface. This technique is used extensively in the electronics industry to construct semiconductor components and printed circuit boards (PCBs). It may, however, be appropriate for many other applications, such as non-reflective coatings on glass optic elements, metalized packaging plastics, and double glazing coatings.
The application of very thin layers or films of material on sensitive surfaces is generally achieved by a sputtering processes. This type of material deposition is achieved by passing a high tension electric current through an inert, low pressure gas, such as argon, which surrounds a donor and recipient material. The high energy plasma created causes rapidly accelerated ions to strike the donor material, displacing its atoms. The donor atoms then strike and adhere to the target or recipient material at an atomic level and create a very thin, even film. DC sputtering is capable of extremely accurate and controllable material deposition on a wide variety of substrate surfaces.
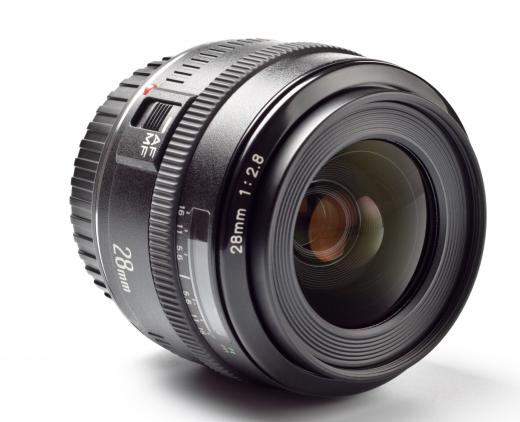
The gas used in the process is maintained at very low pressures, typically in the region of ten thousandths of ambient atmospheric pressure. A high voltage negative DC voltage is then applied to the recipient material via a magnetron. This negative charge attracts the donor atoms displaced by the gas plasma. The technique has no negative effects on the recipient or film materials and is ideal for applications in the semiconductor industry. The highly accurate thin coating made possible with DC sputtering allows for the very precise films required for PCB and component construction.
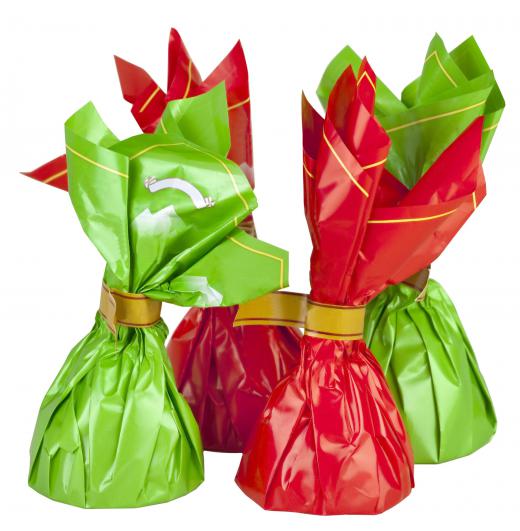
The process is also used in the production of many other coated products. Non-reflective coatings on optics for binoculars and telescopes are applied with this technique, as are those used in double glazed window panes. Plastics, such as those used to package chips and snacks, are also coated with a metallic film with this method. Other common uses of sputtering are the hard nitride coatings on tool bits and metallic coatings on CD and DVD discs. Computer hard drives and solar cells are also coated with various metallic films using DC sputtering processes.