Conformal coating is a layer of material applied to a circuit board to protect it from environmental hazards, particularly if it is going to be used in harsh environments. The coating covers the entire board except for key components to protect it from dust, fingerprints, mildew, mold, and other issues. While it does not completely seal the board, it can offer substantial protection and may reduce the risk of malfunctions caused by leaks and other problems. Conformal coatings are often used in marine and automotive electronics, as well as in devices that may be used outdoors or in extremely cold or hot conditions.
Companies can dip, spray, or brush on a conformal coating, depending on the needs and the equipment. They start by etching the portions of the board to be covered and masking or removing components that need to be exposed. Next, the conformal coating can be applied and then cured in a warm environment before a quality control check to confirm that it is even and correctly applied. Masking can be removed and components reinstalled to finish the product.
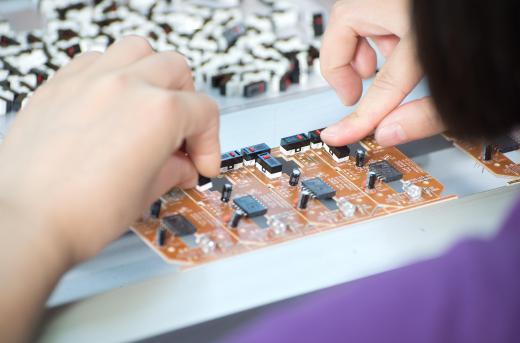
Silicones, epoxies, and parxylenes, among others, can be used to make a conformal coating. Each substance has different advantages and drawbacks that a company can consider when it recommends a coating material. Some are more flexible than others, are better at resisting temperature extreme and corrosions, or have other properties that may be of interest for a particular project. The coating should last the life of the circuit board, unless it is applied incorrectly.
Some manufacturers handle their conformal coating needs during production on their own assembly lines. This can be a cost effective decision when companies have large amounts of materials to process or have special considerations, like the need for extreme confidentiality. Circuit boards are proprietary in nature in some cases and a company may not want to contract out work if it can avoid it, because this could create a security leak.
It is also possible to work with a conformal coating specialty firm to order coatings or to contract out the coating process itself. Such companies focus on this service and may provide very high quality and accuracy standards. Their engineers are often actively engaged in the development of new coatings and the improvement of existing products. This research and development can provide clients with more options than they might be able to access on their own.
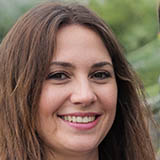
Ever since she began contributing to the site several years ago, Mary has embraced the exciting challenge of being a About Mechanics researcher and writer. Mary has a liberal arts degree from Goddard College and spends her free time reading, cooking, and exploring the great outdoors.