Compression molding is the process of manufacturing by using a mold to produce goods. The mold has two parts that form the complete product shape when they are closed. Materials, which are usually pre-heated, are placed on one of the molds. The two halves are then compressed to spread the material around them. High pressure from the compression distributes the material evenly around the mold cavity.
Heating the material enables it to conform to the mold better. Molds can also be heated to keep the material from cooling too quickly. After the molds are pressed, they are left to cure. The curing process ensures that the material will not change its shape when it is removed from the mold. This process can usually take from several hours to days, depending on the materials used.
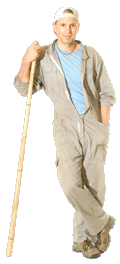
The materials generally used for compression molding are made from plastic compounds, rubber, and metal alloys. Compression molding plastic is commonly made from vinyl or polyester compounds. Before molding, they are usually in the form of pellet, paste, or sheet to ease handling. Additives and fillers may be added to the compound to reduce cost and prevent shrinkage after the molding process.
Compounds that can withstand high temperatures are sometimes used for rubber compression molding. A relatively smooth surface is one of the benefits of this type of molding. This is ideal for the manufacture of products that need to fit tightly, like rubber stoppers.
The automotive industry extensively uses compression molding to produce car parts. Metal alloys are molded to produce fenders and car hoods that have relatively simple shapes. Many other products are make using this process, including plastic cases, electrical equipment, and children's toys.
There are several advantages of using compression molding. The material is commonly in a soft solid state when it is placed on the mold, so the manufacturer can more accurately determine the amount of material inside the compression molding machine. Expensive compounds are used more efficiently through this process. Excess materials — called flash — are the result of material overflowing the mold. They can be recycled by reheating them and adding them back to the process; this saves the manufacturer resource costs.
Another advantage of compression molding is the ability to produce more intricate products. High pressure from the compression forces the material to follow the mold to its exact design. This is best for small and precise instruments, like electronic gadgets.