Centerless grinding incorporates a two-wheel system where a drive wheel pushes the work piece into a grinding wheel and holds it in place until the procedure is complete. It is a process that can cut, shave and shape materials in manufacturing. A common use is in machining tools and other objects. Since centerless grinding does not use a spindle, this procedure allows for a faster operation in many instances where the work piece can simply be loaded and passed through unaided by center chucks.
In traditional or centered grinding, the work piece is located between two spindles and is pushed against a grinding stone to complete the grinding process. In many cases, multiple work pieces can be attached to a table, which is then passed underneath a set of grinding wheels that grind all of the parts to a uniform thickness as they pass beneath the stones.
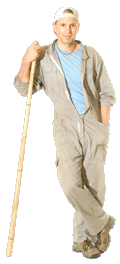
There are three primary examples of centerless grinding used in manufacturing plants around the globe: through-feed, end-feed and in-feed grinding. Each practice has its benefits as well as its negative aspects associated with the particular style. Some of the styles of grinding promote speedy and assembly-line type production methods. Other practices promote accurate grinding at tight tolerances.
Through-feed centerless grinding allows the work piece to be fed rapidly into the grinding wheels and passed through to the next stage of production. The drawback of this system is that only square, right-angle cylinders can be passed through the system.
End-feed centerless grinding utilizes a system where the work piece is drawn between the grinding wheel and the drive wheel. An advantage of this type of grinding is that a more intricate grind can be produced with greater detail than through-feed grinding. The drawback is that the work piece can only become increasingly smaller in the form of a taper.
In-feed centerless grinding allows for the most intricate ground surface and can be comprised of many complex angles and curves. The negative aspect of this grinding style is in the set up time in the shape of the grinding wheel and the time required to place the work in the grinder.
Centerless grinding allows a more complex surface finish than most grinding techniques, which require the work piece to be mounted between two centers. It speeds up production and increases profit for the manufacturer in many instances. The skill of the grinder operator in not only the operation of the machine, but in the set up of the machine is tantamount to the success of the parts run. A great deal of waste can be generated by a non-observant grinder operator.