Blanking is a stage in the manufacturing process where dies are used to punch metal blanks in preparation for processing and finishing. For example, a company manufacturing medals can run a coil of sheet metal through a blanking machine, which cuts out circles which can be stamped with the medal design. Dies used for this process can be generic or custom-ordered for specific projects. This method is used in the production of a range of metal components, from computer parts to precision tools.
Most commonly, blanking is done with a coil of metal. Coils are easier to handle than individual sheets because they are compact when not in active use, and can be loaded into manufacturing equipment for high speed processing. Firms can customize the alloy used in a coil as well as the thickness and width to suit a given project. Larger coils may require processing in special facilities because the blanking equipment may need to be extremely large.
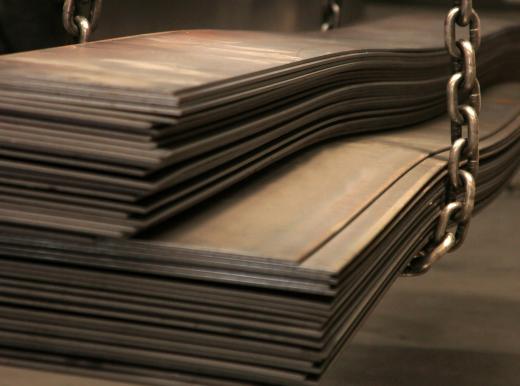
In the blanking phase of manufacturing, the dies punch patterns in the metal, much like a cookie cutter. The cookie, so to speak, becomes the workpiece; it can be stamped with a design, finished to smooth out the edges, and treated if the metal needs a patina or coating. Leftover dough can be recycled for use in other projects. Piercing, the opposite manufacturing processes, punches holes out of a workpiece and discards the contents of the holes as scrap.
Companies can contract out this service if they don’t have the equipment. A firm can provide coils or use those supplied by the customer, and may use its own blanks or custom-produced dies that the customer orders. Costs for commercial blanking can depend on the project. Discounts may be available for high volume orders, because a large part of the cost involves setting up and calibrating the equipment. Additional services can include grinding to remove burrs as well as stamping and polishing, depending on the needs of the customer.
Precision blanking, a related service, yields metal pieces with very tight tolerances. This may be necessary for tools, electrical components, and some other special circumstances. In this case, the blanks cannot vary from the pattern because they might not work correctly; in precision machining, for instance, a tiny marginal difference may mean that two parts won’t articulate correctly. They could be subject to wear-induced damage and failure, which is not desirable.
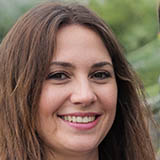
Ever since she began contributing to the site several years ago, Mary has embraced the exciting challenge of being a About Mechanics researcher and writer. Mary has a liberal arts degree from Goddard College and spends her free time reading, cooking, and exploring the great outdoors.