In metal fabrication, autofrettage refers to the process by which metal pressure vessels are subjected to tremendous amounts of pressure in order to strengthen the vessel for industrial use. This process also increases the durability of the metal which constitutes the vessel. The goal of the autofrettage process is to induce compressive residual stress to find the pressure point at which the metal begins to bend. After the maximum elastic limit is found, the pressure vessel is re-examined and reconfigured to increase the amount of compressive residual stress it can handle in future usage, preventing fatigue.
There are several steps to the autofrettage metal fabrication process. First, the metal part is placed in a fixture by either a member of the plant's research and development team or by a machine. Next, a safety shield is used to protect the operator from any byproducts that may be produced from the autofrettage process. Once the shield is secure, the vessel will be filled with water or a petroleum-based substance. Finally, a machine which intensifies pressure will apply pressure to the part, hold for several seconds, and release the applied pressure.
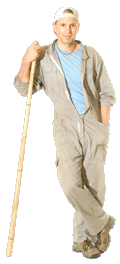
A component has been autofrettaged once this step-by-step process has gone through several cycles. Afterward, research and development scientists record important data, such as the amount of pressure applied, the elastic limit, and more. Specialized software is used to gather information about statistical controls during the process. The autofrettage technique allows the team to pre-stress a series of components and condition them to manage any stress they may undergo while in operation, whether through pressure, temperature, or repetitive usage stress.
Autofrettaged metal undergoes extreme pressure that is high enough to bend the part of pressure vessel, but not high enough to actually crack or otherwise break the part. In addition to usage in industries where pressurized vessels are critical, such as the aeronautical and petrochemical industries, autofrettage is still used in gun barrel manufacturing. In fact, the history of autofrettage begins with the French militia in the 1800s, who used the technique to optimize the durability and shelf life of their gun and canon barrels.
Practical applications of this technique are numerous. It is used to condition heavy tubes which experience repetitive, cyclic loading and thus are prone to wear and tear. Popular components which utilize these sort of heavy tubes include: fuel rails and fuel lines, hydraulic cylinders, oil field components, waterjet cylinders, and check valves.