Many metals are structurally weakened by the oxidation process, but not aluminum. Aluminum can actually be made stronger and more durable through a process called 'anodizing'. Anodizing involves placing a sheet of aluminum into a chemical acid bath, quite often acetone in laboratory experiments. The sheet of aluminum becomes the positive anode of a chemical battery and the acid bath becomes the negative. An electric current passes through the acid, causing the surface of the aluminum to oxidize (essentially rust). The oxidized aluminum forms a strong coating as it replaces the original aluminum on the surface. The result is an extremely hard substance called anodized aluminum.
Anodized aluminum can be nearly as hard as diamond under the right anodizing process. Many modern buildings use anodized aluminum in places where the metal framework is exposed to the elements. Anodized aluminum is also a popular material for making high-end cookware such as frying pans and pots. Heat is distributed evenly across anodized aluminum, and the process of anodizing provides a naturally protective finish. It is possible to use another electroplating process to make anodized aluminum look like copper or brass or other metals. Special dyes can also be used to color the anodized aluminum for decorative uses.
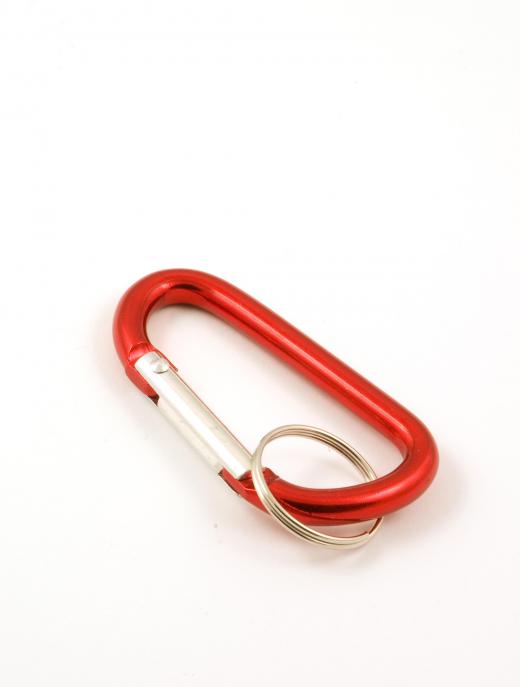
Because of its strength and durability, anodized aluminum is also used in a number of other applications. Many of the satellites circling the Earth are protected from space debris by layers of anodized aluminum. The automobile industry relies heavily on anodized aluminum for trims and protective housings for exposed parts. Furniture designers often use anodized aluminum as the framework for outdoor pieces as well as the base metal for lamps and other decorative items. Modern home appliances and computer systems may utilize anodized aluminum as protective housing.
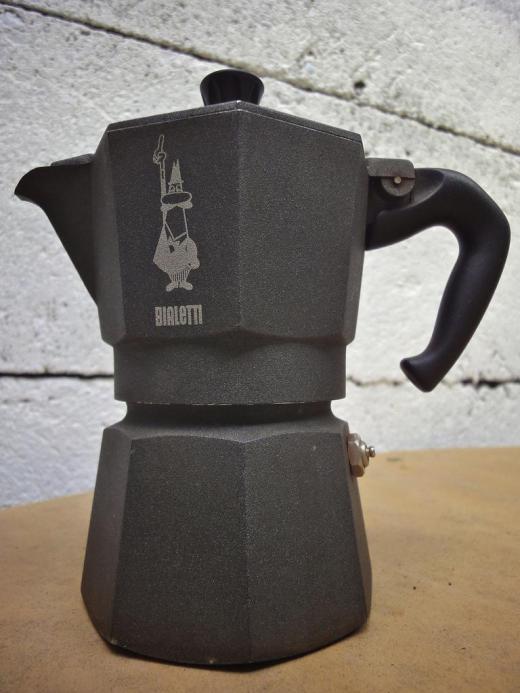
Anodized aluminum may not be appropriate for all applications because of its non-conductive nature. Unlike other metals such as iron, the oxidation process doesn't seem to weaken aluminum. The layer of 'aluminum rust' is still part of the original aluminum and will not transfer to food or easily flake off under stress. This makes it especially popular for food-service applications and industrial applications where durability is crucial.
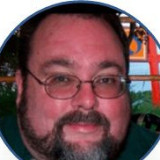