Anodic bonding is a method of wafer bonding that is widely used in the microelectronics industry to seal together two surfaces using a combination of heat and an electrostatic field. This bonding technique is most commonly used to seal a layer of glass to a silicon wafer. Also called field assisted bonding or electrostatic sealing, it resembles direct bonding in that — unlike most other bonding techniques — it normally requires no intermediate layer, but it differs in that it relies on electrostatic attraction between the surfaces resulting from the movement of positive ions when a high voltage is applied across the components.
It is possible to use anodic bonding to bond metal to glass and, employing a thin intermediate layer of glass, silicon to silicon. It is particularly suitable for silicon-glass bonding, however. The glass needs to have a high content of alkali metals such as sodium to provide mobile positive ions; a specific type of glass that contains about 3.5 percent sodium oxide (Na2O) is often used.
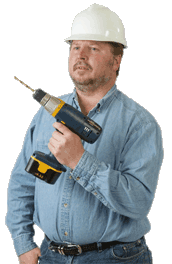
In the bonding process, the surfaces of the two components are smoothed and thoroughly cleaned to ensure close contact between them. They are then sandwiched between two electrodes, heated to 752-932° Fahrenheit (400-500° Celsius), and a potential of a few hundred to one thousand volts is applied, such that the negative electrode, which is called the cathode, is in contact with the glass, and the positive electrode, the anode, is in contact with the silicon. Positively charged sodium ions in the glass become mobile and move toward the cathode, leaving a deficit of positive charge near the boundary with the silicon wafer, which is then held in place through electrostatic attraction. Negatively charged oxygen ions from the glass migrate toward the anode and react with the silicon when they reach the boundary, forming silicon dioxide (SiO2); the resulting chemical bond seals the two components together.
The technique is used for the encapsulation of sensitive electronic components to protect them from damage, contamination, moisture and oxidation or other undesirable chemical reactions. Anodic bonding is particularly associated with the micro-electro-mechanical systems (MEMS) industry, in which it is employed to protect devices such as micro-sensors. The main advantage of anodic bonding is that it produces a strong, permanent bond without the need for adhesives or excessively high temperatures, as would be required to fuse the components together. The main disadvantage of anodic bonding is that the range of materials that can be bonded is limited, and there are further limitations on the combinations of materials, because they need to have similar thermal expansion coefficients — that is, they need to expand at similar rates when heated, or differential expansion might cause strain and warping.