An oriented strand board panel, or OSB for short, is a wood product made from strands or flakes of wood that have been compressed and glued together to form a strong wooden sheet or panel. The wood used to create OSB panels typically comes from fast growing species of trees such as yellow pine and bamboo. Also known as waferboard, these panels are widely used in the construction industry, particularly for sheathing, subflooring, and roofing. OSB panels are available in different sizes and thicknesses, including 4 feet x 8 feet x 0.5 inches (about 1.2 meters x 2.4 meters x 1.3 centimeters).
OSB panels are manufactured by compressing layers of strands of wood that are bound together with wax and resin adhesives. The strands themselves are small and are layered in a criss-crossed fashion. The thickness of an OSB panel varies, though they are typically about 0.5 to 0.75 inches (about 1.3 to 1.9 centimeters) thick.
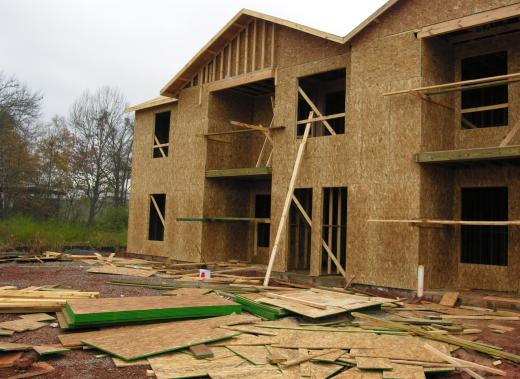
The compression of the wooden strands is typically achieved with the use of a thermal press. During the process of compression, the strands are bound together with the help of waterproof and oil-proof resin, heat and pressure. This process helps avoid internal gaps or spaces which, in turn, helps ensure a rigid, strong, and water-resistant product.
This compression process results in large OSB mats which are then cut into individual panels and packed for marketing. Borate-modified wood products used in OSB panels help protect the panels from termites, mold, and fungus. Moreover, the resins used in the OSB panel emit very low levels of formaldehyde.
To the layperson, an OSB panel might look much like plywood or particle board. In fact, the three products are used for many of the same purposes. There are some important differences, however. OSB is cheaper than plywood because it can be made from small pieces of wood, rather than the large sheets of wood that plywood is made from. This means that OSB can be harvested from younger, faster growing trees than plywood. Both particle board and plywood have smoother finishes than OSB and therefore are better suited for uses that require a smooth finish.
Newer OSB panels are resistant to warping and swelling. Isocyanate resins used in forming these panels help bind the strands together without the need for considerable compression, producing lighter panels. Sealants are applied to the edges of an OSB panel to help prevent water from entering through the sides. As a result, OSB panels typically have long lives with some manufacturers giving guarantees of up to 50 years.
There are different types of OSB panels. Some common types include the OSB sandwich panel, OSB tin/zinc coated roofing, OSB fiber-cement siding, OSB wooden beam, and OSB floor panel. OSB subfloor panels have tongue and groove edges to interlock them while subflooring.