An induced draft is a type of mechanical draft that is produced as a means of moving air or other types of gases through a process. The draft is often created and managed with the use of fans or suction to achieve the desired rate or pace of the draft, and to sustain that pace for as long as desired. The concept of the induced draft is common with the function of boilers, making it possible to control both the direction and the speed of the draft to generate the optimum results.
Creating an induced draft can be managed in more than one way. One approach involves positioning a steam jet that induces the air or gas within a flue, effectively forcing the gases through the system at a more rapid pace. This particular approach was often used with steam locomotives that were constructed with smaller chimneys, allowing for more efficient use of the steam used to drive the locomotive forward. An alternative to the steam jet is a simple fan that sucks the air or gas through the mechanism and forces it through a flue at a faster pace than would be possible using other means of managing the draft.
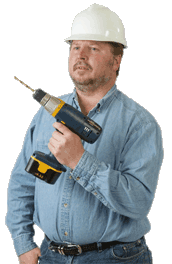
An induced draft offers a couple of benefits over the more traditional natural draft. One has to do with controlling the speed of the air movement. While the natural draft is subject to a wider range of air conditions, the induced draft can be controlled and the impact of those outside factors minimized significantly. By using fans or some sort of jet stream, it is possible to adjust the movement, and even to maintain that movement at a constant pace. This helps to produce results that are easier to track and measure, which in turn aids in determining if the boiler is working at the highest level of efficiency.
The use of an induced draft is seen in a wide range of applications. Heating and air conditioning systems use the concept to distribute hot or cold air throughout a structure with more efficiency. Boilers that rely on ductwork to distribute hot air to radiators that are connected with the ductwork may also use fans to direct the flow and keep the supply of heat constant. While usage of some mechanism to push the air in a specific direction does require the addition of more equipment, the higher rate of efficiency often translates into utilizing less energy which in turn means lower operating costs for the equipment in general.
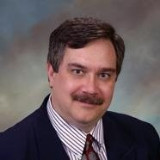