An electrohydraulic actuator is a device designed to provide switching or actuation for a variety of systems using hydraulic force that is constantly regulated by feedback from system sensors. This level of actuation control is necessary in systems that feature constant demand fluctuations. The actuator control is made possible by the inclusion of a servo system that assimilates sensor inputs and regulates the flow of hydraulic fluid to the actuator. Beyond this feature, the electrohydraulic actuator functions in much the same way as other fluid-driven actuators and consists of a piston in an enclosed tube or sleeve driven forward or back by fluid pressure. This type of actuator is typically available in linear, quarter-turn, and multi-turn configurations.
Most conventional actuators use electric motors or the pressure of compressed air and oil to move a mechanism that, in turn, provides actuation for another mechanism, such as a valve, shutter, or switch. In these cases, the actuator supplies a fairly simple movement of finite magnitude. In other words, it will move a shutter set from the closed to open position only with no intermediate positional control. Many system processes do require a higher degree of fine actuator control, both in terms of the distance that the actuator moves and in the amount of power applied. When hydraulic actuators are used, one of the ways of achieving this type of control is the use of an electrohydraulic actuator.
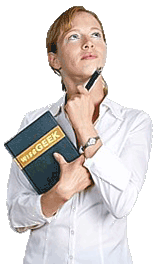
The electrohydraulic actuator shares many similarities with other hydraulic single-duty cycle variants in that it consists of an oil reservoir and pump that feeds compressed hydraulic oil to an enclosed piston. The pressure of the oil moves the piston, which supplies the actuation movement. Unlike the simpler single-action actuators, however, an electrohydraulic actuator constantly adjusts to system demands in increments of commensurate magnitude. This wide range of operational movement is made possible by including a servo amplifier and valve set in the actuator circuit. System sensor inputs are sent to the amplifier, which interprets the system requirements and sends corresponding signals to the servo valve set.
The servo valve then acts as a regulator that controls the duration of the movement made by the electrohydraulic actuator, the speed at which it moves, and the amount of torque or power that it exerts. These actuators are available in several configurations, which include linear, quarter-turn, and multi-turn types. The linear actuator exerts the actuation movement in a straight line, while the other two types feature rotary actions. The quarter-turn actuator is typically used on butterfly-type valves that require only a quarter-turn to operate, and the multi-turn variety on gate-type valves that require one full turn or more to open or close.