A wire conveyor belt is a component used on some types of conveyor systems to facilitate movement of items or materials from one fixed location to another within a space. The wire conveyor belt is an alternative to a rubber or plastic belt; it is made of metal wire woven together to create a belt that is durable and resistant to heat. It is also easily cleaned, and it allows for plenty of aeration or ventilation for items being transported on the belt. Such belts are often used in food processing applications.
Steel is usually the material of choice for construction of a wire conveyor belt, though aluminum can be used as well. The steel is woven into a belt shape, leaving gaps between rungs or steel mesh. These gaps allow for better drainage, ventilation, and cleaning. Certain grades of steel are also appropriate for food processing applications because the steel will not contaminate the food being transported. A wire conveyor belt is also less likely to stretch or wear quickly, as is the case with a rubber belt. The metal belt can be propelled using a track system, thereby improving grip and reducing slippage, while a rubber belt must be run around rollers and it must be tensioned frequently to prevent slippage.
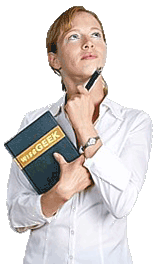
There are some disadvantages to a wire conveyor belt. The belt is likely to be more expensive than a rubber belt, and if the mesh does get damaged, repair can be difficult. The entire belt may need to be replaced instead of repairing that one part of the mesh. The weight of the wire conveyor belt will also be substantially higher than the weight of a rubber or plastic belt, which means the conveyor motors will need to work harder to move the belt as well as the items loaded on it. While the gaps in the wire mesh can be an advantage, they can also be a disadvantage because fine particulate matter will be able to fall through the belt, potentially damaging components beneath.
The design of the wire conveyor belt can vary significantly according to its intended application. Sometimes the mesh is woven quite loosely to create larger gaps, while in other cases, the mesh may be wound tightly to prevent larger gaps. Sometimes slotted gear wheels or pulley wheels are used to pull the wire belt itself, whereas in other cases a cog may propel a specially designed track on the side of the wire belt.
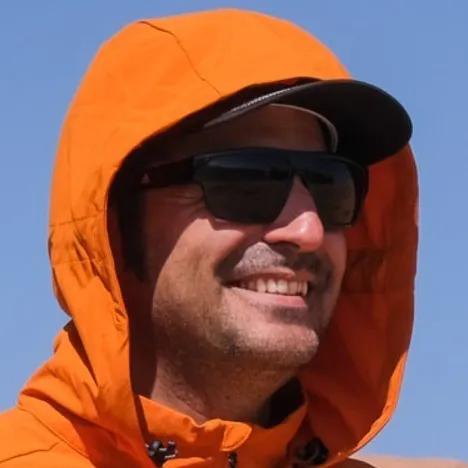