A volute is the name for the portion of a centrifugal pump that sits just past the impeller. This portion of the pump decreases the speed of the water flowing through the system while increasing its pressure. This balances the pressure on the pump’s shaft, reducing wear. Volutes are easy to recognize, as they increase in size as they move away from the impeller, giving them an upside-down, funnel-like appearance.
Centrifugal pumps use a bladed impeller to increase the pressure and speed of water. Water enters the system and is caught up in the spinning impeller blades. These blades push the water into a connected chamber at a much faster speed than when it entered. This connected chamber, the volute, widens as the water moves away from the impeller. This decreases the water’s speed while maintaining the increased pressure generated by the impeller.
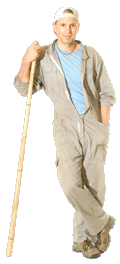
The volute chamber works using a very simple fluid principle—liquid slows down as it widens out. If a mountain stream is only a few feet or meters wide, the water flows very fast, but when that same stream widens out to three or four times its original size, the water slows down. In this case, the pressure on the water also decreases, because the water is free to move as it wants.
This is not the case in a volute. These chambers collect water that is moving quickly and allow it to slow down in a very short period. Since the water is unable to move as it wants like the stream, this process effectively transfers the kinetic energy of the moving water into stable pressure in the system. The fast-moving water pushing against the slower-moving water generates this increase in pressure. As long as the water feed is constant, the pressure doesn’t change.
These types of pumps are common in systems where a lot of liquid is constantly moving, like a water pump on a city pipe. As long as the impeller is in operation, the flow needs to remain constant to keep a stable pressure. As a result, systems that only move liquid occasionally will use different styles of pumps.
When the water pressure isn’t constant, there are three common results. The first effect is damage to the impeller system through uneven water pressure on the blades and shaft. Next, liquid on the volute side of the pump will have sharply-decreased pressure. Lastly, air will often enter the system, potentially damaging the siphon effect and causing the liquid to stop flowing.
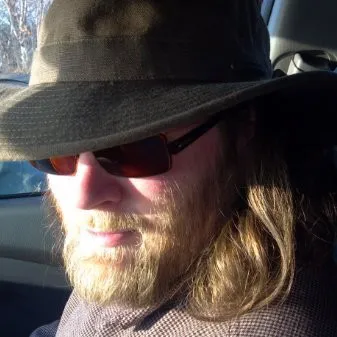